本文是一篇硕士论文,硕士论文是攻读硕士学位研究生所撰写的论文。它应能反映出作者广泛而深入地掌握专业基础知识,具有独立进行科研的能力,对所研究的题目有新的独立见解,论文具有一定的深度和较好的科学价值,对本专业学术水平的提高有积极作用。(以上内容来自百度百科)今天为大家推荐一篇硕士论文,供大家参考。
第1章绪论
1.1研究背景及意义
氢气作为化工生产中重要的原料,已广泛地用于光导纤维的制造、半导体的生产、非晶太阳能电池的制造;大型化学工业,如合成氨等,以及大型石油企业的加氢原料气[1-2]。由于氢气具有对环境无污染,燃烧热值高等特点,被认为是21世纪最具应用前景的清洁能源[3]。对于氢气的制取,尤其是对于高纯度的氢气的制取目前已经成为科研和工程化应用研究的热点。近年来随着低品质原油加工量的增加和环保法规对燃料清洁度要求的不断提高,炼油厂对氢气的需求大幅增加。某炼化企业炼油厂原油一次加工能力1000万吨/年,催化加工能力280万吨/年,加氢加工能力490万吨/年。催化装置和加氢装置排出的干气中含有非常可观的氢气,如果将其作为燃料烧掉,每年要烧掉纯氢约3500吨。公司考虑充分利用这两套装置的干气,同时,炼油优化增产丙烯项目中催化裂解(以下简称“TMP”)装置投产后,全厂干气量将达到33万吨/年,氢气含量约1.0162万吨。如果将干气中的氢气提纯出来,既可满足目前加氢装置的需要,又能充分利用资源。而且,炼厂气综合利用是贯彻我国政府提出的“节能减排”方针的重要举措。随着国家将节能减排工业做为经济结构调整的首要任务,不断加大政策的执行力度,炼油行业直接燃烧炼化干气势必造成资源的浪费。因此,炼油企业需要重视炼化干气中可回收利用成分(如:氢气),想方设法利用起来增加经济效益,走节能减排的循环经济发展道路,以减轻对大气的污染,及改善企业自身及周边生态环境。因此,公司积极进行了炼厂干气提氢的方案论证工作,利用催化干气、加氢干气以及TMP干气资源,建设一套33万吨/年干气提氢装置。装置投产后,每年可为公司输送高纯氢气1.0162万吨,既可以提高企业效益,又解决了氢气不足的问题。综上所述,该项目具有较好的节能效果,也具有重要的环保意义。
.........
1.2干气提氢概念
对于炼油厂而言,所说的“干气”主要是来源于原油的二次加工装置中富含轻组分的气体,如催化裂化、热裂化以及延迟焦化等装置,其中产生量最大的为催化裂化装置[4-5]。干气的主要组成成分为:氮气(N2)、氢气(H2)、甲烷(CH4)、乙烷(C2H6)、乙烯(C2H4)等[6],目前对于干气中的有效物质进行回收中存在的限制条件为:缺少完整有效的氢气分离回收以及进行综合利用技术,炼化企业常把干气用作为二次燃料气或直接燃烧后放空处理,这样的处理方法不仅对环境带来巨大的危害和污染,对于解决当前资源紧缺问题更没有任何作为[7]。干气制氢通常是指:以干气为原料,采用加氢技术将原料中的烯烃饱和为烷烃,并将有机硫、有机氯等杂质转化为无机硫、无机氯,再通过脱氯、脱硫反应器脱除HCl和H2S,使精制后的气体硫含量小于0.5ppm,氯含量小于1ppm,烯烃含量小于0.1%(v)。精制后的原料采用水蒸汽转化工艺将烃类转化为H2、CO、CO2,转化气中的CO采用中温变换,使其反应生成H2和CO2,变换气中的残余CO、CO2和CH4等杂质,采用变压吸附(PSA)的净化技术进行清除,从而得到纯度为99.9%(v)、CO+CO2<20ppm的产品氢气。而当前,国内的炼化企业干气主要用在以下几个方面:①制备乙苯。对于催化裂化所产生的干气,可以不需任何特殊的精制,用作与苯进行烃化反应以制取乙苯的。相关的对比研究试验结果表明,利用干气比用聚合级乙烯为原料制取乙苯,其工艺成本可降低6.2%左右。②提取氢气。轻烃水蒸气和变压吸附分离(PSA)是目前干气制备氢气的主要技术路线,国内已有相关企业采用这种方法从干气中提取分离氢气。③制备环氧乙烷。催化裂化所产生的干气可作为生产环氧乙烷的的原料,目前环氧乙烷制取工艺技术路线为乙烯在银催化剂作用下的氧化法。环氧乙烷是乙二醇、乙醇胺以及乙二醇醚等原材料。④制备二氯乙烷。从催化裂化产生的干气中分离得到的乙烯,可作为制取二氯乙烯的原料。乙烯在经过脱水和脱除H2S步骤后,可和氯气在相关的条件下进行反应得到二氯乙烷。⑤制备氮肥。早在20世纪70年代初,已有科研生产单位开发出了可以利用干气进行合成氨的相关工艺技术研究:将催化裂化所产生的干气用于部分替代或全部替代石脑油而作为生产氮肥的原料,经测算1t催化裂化干气可代替0.889t石脑油。⑥精制乙烯。变压吸附可作干气中乙烯分离精制的有效手段,中石油兰州石化公司应用变压吸附分离方法对催化裂化干气中的乙烯和乙烷进行提取分离,可得到乙烯40.5kt/a、乙烷10.0kt/a,以此可替代裂解原料石脑油128.0kt/a,产生的经济效益为1.35亿元/a。
..........
第2章国内某石油化工企业处理干气的工艺技术
2.1干气提氢装置气源
本文所提到的某石油化工企业干气提氢装置的原料来源有两路:一是三套加氢车间低分干气、汽提塔干气汇总到干气脱硫塔,经过贫胺液脱硫后而得到的脱硫干气,总量约为6000Nm3/h,其中氢气含量约50%,其成分如表2-1所示;二是三套催化裂化车间产生的干气,经脱硫塔脱硫后得到的脱硫干气,干气量约14000Nm3/h,其成分如表2-2所示,氢气含量约22%。混合后进入干气提氢装置,混合后其成分如表2-3所示,其中氢气含量32%,其中后续工艺要求硫含量不得高于50ppm。根据某石油炼化企业混合干气的原料特点以及企业对产品氢的质量要求,单独单一分离技术,对产品氢的回收率都不高。若采用章节1.4.2所述的串联流程,即对浓度为32%的混合干气用膜分离技术来进行提纯,氢气含量≥79.02%,产品氢回收率>90%;然后再用VPSA把氢气由79.02%提浓到99.41%,VPSA的氢气回收也设为90%。可计算得出某石油炼化企业采用膜分离技术+VPSA技术串联工艺所得出的产品氢浓度达到99%,产品氢总回收率>80%。
.........
2.2干气提氢装置工艺概述
自系统管网来的催化干气、加氢干气混合后进入装置,经过快速切断阀UV-1101后,进入K101干气压缩机。经过干气压缩机K-101A/B二级压缩,介质压力升到1.0MPa(G),进入E-101降温冷却,需要注意的是,工艺介质在E-101中冷却,控制冷后温度不大于40℃。冷却后的原料气进入分液罐D-105,除去含有的液滴,气体进入聚结过滤器F-201A/B,在F-201A/B聚结过滤器中脱去工艺介质中的液相及含有的杂质;过滤后的工艺介质依次进入E-201膜前换热器、E-202A/B膜前加热器,最终将工艺介质温度提升到80℃左右。加热后的工艺介质进入M-201A1-P4膜分离器系统,经过M-201A1-P4膜分离器系统分离后,混合干气最终被分离为两路,其中一路为非渗透气(贫氢气流,直接排入瓦斯管网)经调节阀PV-2201进入非渗透气冷却器E-204,冷却至40℃后,并入解吸气至瓦斯管网。另外一路为渗透气,经E-203A/B富氢冷却器冷却至40℃后进入富氢压缩机入口缓冲罐D-102。氢气(纯度≥99%(mol)):由于WH-15B专用吸附剂的作用,可以将工艺介质中包含的CO2、N2等大分子杂质聚集在其表面,从而得到高浓度的氢气送至脱氧干燥系统,经C-301吸附塔、C-401脱水塔、R-401脱氧塔进一步深度脱去工艺介质中所含的水、氧气,得到达标氢气,氢气纯度大于99.0%。VPSA顺放气:富氢气经过两次顺放,得到顺放气,该气体并入膜回收富氢气管线,返回富氢气压缩机入口,与膜分离系统分离出来的渗透气一起进入K-102A/B/C富氢压缩机进行再利用。
.........
第3章国内某石油化工企业炼化干气膜分离过程的研究.............28
3.1膜技术干气提氢新工艺原理...........28
3.2膜分离工艺设备的工艺流程确定及模型计算.............30
3.3膜分离干气提氢新工艺特点及其分离效果.......34
3.4本章小结.............36
第4章干气膜分离渗透气的变压吸附纯化过程研究...........38
4.1变压吸附技术原理.......38
4.2变压吸附工艺参数确定.........43
4.3变压吸附分离工艺流程的确定.......47
4.4变压吸附后脱氧工艺.............49
4.5本章小结.............49
第5章膜+VPSA组合干气提氢新工艺的安全性和故障分析..........51
5.1变压吸附工艺可靠性及关键设备.............51
5.1.1变压吸附工艺可靠性.....51
5.1.2干气提氢装置真空变压吸附(VPSA)单元的关键设备程控阀...........51
5.2程控阀的结构和原理.............52#p#分页标题#e#
5.3程控阀故障原因及危害.........52
5.4膜+VPSA组合干气提氢新工艺工程应用可靠性措施............54
5.5本章小结.............55
第5章膜+VPSA组合干气提氢新工艺的安全性和故障分析
5.1变压吸附工艺可靠性及关键设备
5.1.1变压吸附工艺可靠性
干气提氢装置真空变压吸附(VPSA)单元工艺技术,即装置由吸附塔C-301A~F组成。工艺过程由塔内吸附、塔内均压降压、塔内顺放、塔内逆放、塔内抽真空、塔内均压、塔内升压和氢气最终升压等反应步骤组成,具体工艺过程如下:原料气来的压力为2.7Mpa,进入原料气气液分离器分液后,自塔底进入吸附工况的吸附塔,除去氢以外的杂质,获得纯度>99%的氢气,送往脱氧干燥单元。当介质在吸附塔内达到饱和后,则吸附剂停止对介质的吸附,从而转入再生过程。干气提氢装置真空变压吸附(VPSA)单元程控阀门的可靠性是本套装置整体安全保障的关键。干气提氢装置真空变压吸附(VPSA)单元工艺特点要求:程控阀门开关频次高,阀门密封组件密封性能要高。程控阀是由阀体,阀芯、密封组件、气缸、活塞、支架等组成。程控阀最关键的部件就是密封组件,密封组件材料多为柔性石墨,采用V型圈自锁式密封形式。程控阀阀体一般采用铸钢,阀体生产要求具备多重耐压性,阀芯要求耐冲刷性能强。当仪表动力风进入缸体一面时,推动活塞在气缸内做往复运动,带动阀芯上下运动达到阀门快速开关的作用,从而达到输送工艺介质的目的。如图5-1所示,该程控阀的控制系统由气源、电磁换向阀、气动执行机构、电气控制系统等一些列控制组件构成。
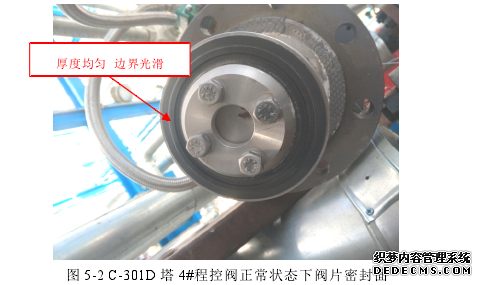
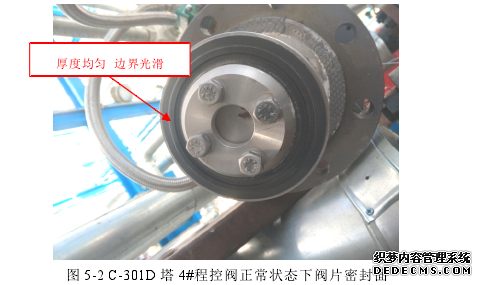
........
结论
公司干气提氢装置是集经济效益与环保效益于一体的生产装置,本文通过对影响干气提氢装置分离能力研究,找到了提高氢气产出和纯度的方法措施,获得的结果如下。
(1)对影响干气提氢氢气分离效果的因素进行研究,并经过实际生产的验证,对干气提氢装置主要控制参数进行了确定,尤其是对变压吸附工序吸附时间给出了最优的时间设定,使变压吸附工序达到氢气收率、合格率和产量平衡的效果。
(2)装置一年来的生产经验,证明本文所研究的干气提氢膜回收与变压吸附相结合新工艺不仅可以使含低氢气浓度的干气提氢成为可能,而且提纯的氢气浓度高达99%以上,并且产量稳定,环保效益高。本装置目前每年运行8000小时,年产氢气4800吨,回收干气16万吨/年,减少CO2排放量32万吨,年产效益约为35112万元,获纯利润5200万元;以设备投资24679万元计算,该项目当年即可收回成本。且本装置所采用的工艺技术投资少、能耗低,易于操作与维护,同时产品质量高、物耗、能耗低,有利于环境保护。
(3)对干气提氢装置的研究,初步证明了膜回收与变压吸附相结合的新工艺,技术先进,提纯纯度高,对炼厂生产有极大的意义。
..........
参考文献(略)