本文是一篇硕士论文,硕士是一个介于学士及博士之间的研究生学位(Post-Graduate),拥有硕士学位者通常象征具有基础的独立的研究能力。(以上内容来自百度百科)今天为大家推荐一篇硕士论文,供大家参考。
1 绪 论
1.1 课题研究背景及意义
发动机是整车的关键零部件,在整车系统中处于至关重要的一环。而缸体是发动机最基本的零部件,它与发动机的曲柄连杆机构、进排气机构、润滑、冷却等零部件组合成一个完整的系统。缸体支撑频繁往复运动的活塞、高速旋转的曲轴等部件,其加工质量直接影响发动机的性能和使用寿命。汽车发动机缸体为箱体类零件。其加工包含了较多的端面和孔系,工艺体系较复杂,在保证加工效率的同时,加工质量难以得到保证。缸体的制造加工主要分为平面加工与孔加工,平面加工由端面铣削来完成,孔加工一般由钻、绞和镗削等加工工艺来完成。缸体生产线上不同的加工部位及不同的加工方式均是在不同的工装夹具、刀具、走刀路径及切削参数下完成的,复杂的工艺导致某些重要工序加工问题较为突出,比如刀具异常损耗、精度超差等常见问题。这些问题不仅影响生产节拍,而且导致生产成本急剧上升。本文以上汽通用五菱公司发动机缸体生产线为研究背景,经调研发现,其生产线上刀具异常损耗的问题较为严重。例如,缸体各端面的加工通常由铣削来完成,由于各端面切削区域较多,切削面积较大,为了保证生产节拍通常采用比较激进的切削参数,导致切削力较大,铣削过程切削热不易传散,因此切削效果不理想,加工过程中易引起切削过载,俗称“闷车”现象,如图 1-1。另外,钻孔过程由于排屑困难,容易出现钻头受力不均或者卡死的现象,使得钻削载荷急剧增大引发钻头断刀,如图 1-2。钻头断刀本质上也是一种加工过载现象。
...........
1.2 汽车发动机缸体加工工艺与加工现状概述
五菱发动机缸体生产线是一条自动化程度高的敏捷柔性化生产线。其工艺流程参考了缸体结构特点,设计成不同的加工阶段,各个生产加工环节紧密相连,在生产节拍的控制下,每一台数控加工中心连续完成数道加工工序,整条生产线实现毛坯上线到输出缸体成品。根据缸体的加工特点,将发动机缸体从毛坯上线到成品下线按照粗加工-半精-精加工的工序划分原则,将其加工工序分为 3 阶段:主要型面加工阶段(OP10-OP60,即粗加工阶段)、辅助结构加工阶段(OP70-OP110,即半精加工阶段)和重要孔系加工阶段(OP170-OP200,即精加工阶段),其具体加工工艺流程如图 1-3 所示。另外,目前提供 N12 型号缸体毛坯的供应商主要有 A、B 两厂家。两毛坯供应商提供的不同毛坯在实际生产过程中差异明显。为了节省成本,SGMW 更换了毛坯供应商,原先主要由 B 厂家提供的 N12 机型毛坯大部分换成了 A 厂家提供的毛坯,换用毛坯过后发动机缸体生产线 M1/M2 重点工序刀具寿命显著下降,如图 1-5。从 A 厂家与 B 厂家刀具寿命对比发现,其中 OP20 工位刀具 T201/T261(铣刀)的寿命均有较大下降,T261刀具寿命更是由原先加工 B 厂家毛坯的 224 件骤减到加工 A 厂家毛坯的 65 件;OP170工位刀具 T22086(钻头)寿命下降也较明显。如此频繁的异常换刀,严重降低了加工效率,刀具成本也急剧增加,成为五菱亟待解决的问题。为进一步分析频繁换刀的原因,统计并分析 OP20 工位铣刀 T261 的换刀数据,发现 T261 因“闷车”引起的换刀占据了 80%以上,如图 1-6 所示。OP170 工位 T22086 加工曲轴后油封定位孔经常出现钻头卡死或断刀的情况。由上述论述可知,换用 A 厂家毛坯过后加工过载是造成刀具寿命显著下降的主要原因。
.........
2 缸体毛坯材料性能差异对切削载荷的影响分析
2.1 引言
由第一章论述可知,不同缸体毛坯供应商提供的毛坯在实际生产过程中差异明显。相比加工 B 工厂的缸体毛坯,A 工厂的缸体毛坯上线后,M1/M2 生产线重点工序加工过载现象频现,刀具寿命下降较为明显。因此有必要对两厂家提供的缸体毛坯材料性能进行对比分析,判断其材质灰铸铁力学性能的高低。铸铁的金相组织对其力学性能起着决定性作用。铸铁的金相组织由基体组织和片状石墨组成,片状石墨的形状特点、尺寸、数量在基体组织中的分布情况将直接影响铸铁的力学性能。此外,碳化物、硫化物等非金属化合物含量虽少,但对其强度和硬度仍有一定的影响。而石墨、基体组织的数量和形态分布与铸铁的熔炼技术密切相关,如铸铁熔炼过程中的化学成分、冷却速度等条件不同,就会出现形状特点、尺寸数量不同的石墨形态,不同类型的基体组织,进而产生不同的材料性能。不同性能的灰铸铁有不同的力学性能,差异可从缸体硬度、切削性能等方面体现出来。现重点分析两种缸体毛坯化学成分的差异、金相组织的差异,进而判断切削性能的优劣。
...........
2.2 缸体毛坯材料性能对比实验与分析
为了完成 A、B 两类缸体毛坯件灰铸铁材料性能的对比研究,本文将进行材料元素分析、金相组织观察、缸体毛坯布氏硬度测试以及相应的切削实验。合理地选取实验设备关系到实验的有效性和结果分析的可靠性。下面对重要的实验设备进行简要介绍。光学金相显微镜,如图 2-3。金相显微镜用来观察研究材料的显微组织。显微组织包含了晶粒结构、化合物、相变转变物等微观组织。由此可以用来研究元素成分与微观组织之间的变化对应关系,可以为分析加工缸体加工过载现象提供依据,还可对缸体毛坯进行质量控制和产品检验。
........
3 缸体后端面铣削过载分析与走刀路径优化 ........... 29
3.1 缸体后端面铣削实验........... 29
3.2 缸体铣削力经验模型........... 32
3.3 缸体后端面铣削加工过载分析 ..... 37
3.4 考虑铣削载荷的走刀路径优化 ..... 41
3.5 走刀路径优化方案实验验证 ......... 43
3.6 本章小结 .......... 48
4 缸体钻削加工过载分析与工艺参数优化 ..... 50
4.1 引言 ........ 50
4.2 缸体钻削实验 ............ 50
4.3 钻削力经验模型......... 54
4.4 直槽钻加工过载分析........... 57
4.5 缸体钻削加工参数优化....... 61
4.6 本章小结 .......... 63
5 结论及展望............. 64
5.1 结论 ........ 64
5.2 展望 ........ 64
4 缸体钻削加工过载分析与工艺参数优化
4.1 引言
在发动机加工制造过程中,有大量的加工属于钻孔加工。据统计,发动机的缸体、缸盖、曲轴加工所用刀具中,钻头的使用量超过三分之一。钻孔作为机加工中最常用的加工形式,其特点简单高效,且成本较低。但缸体生产线上经常会遇到钻头崩刃、断刀等刀具失效的问题,这些失效往往会造成刀具损坏、工件报废,严重情况下会损坏夹具及机床。从加工特点上看,钻头在钻孔过程中,切削刃受到的转矩最大;钻尖横刃处与工件切除区域挤压变形,受到的轴向抗力较大。当排屑不畅时,容易导致钻孔扭矩过大,钻头被扭断;或者由于钻头修磨不完整均匀性较差,刃口处存在细微的裂纹,当钻头切削刃部分受力较大时引发崩刃,最终导致断刀。因此,从实质上讲,钻头异常断刀的现象也是加工过载引起的。钻削过程中通过切削液将切屑冲出,并保证切削区域冷却与润滑性。如若切屑不能顺利排出,切屑变形及摩擦产生大量热量,会增加刀刃及支承的摩擦磨损,引起钻削扭矩和轴向载荷急剧增大,最终发生断刀。由于直槽钻加工内孔精度高,理论刀具寿命相对长于螺旋钻,故内冷直槽钻在发动机缸体钻孔加工中占据了半壁江山,即钻头内部有一道通槽,称为冷却槽,冷却液在一定的压力和流量的作用下由冷却槽抵达钻尖,将切屑冲出,并起到冷却润滑作用。但是经发动机缸体生产线上调研发现,直槽钻断刀率高于螺旋钻断刀率。其中,M1 OP170 工位 T22086 刀具钻削缸体后端面后油封销孔时断刀率较高。故本章以 OP170 工位 T22086 为研究对象,对比直槽钻、螺旋钻钻削特点,分析直槽钻加工过载原因并给出优化措施。
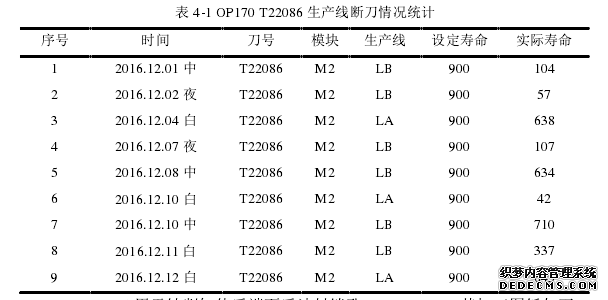
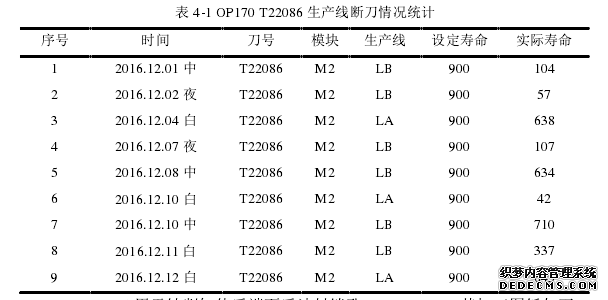
..........
结论
针对上汽通用五菱公司汽车发动机缸体生产线上铣钻削加工过载现象进行了分析,对铣削“闷车”和钻削“断刀”现象提出了相应的优化措施。主要工作包含:探究生产线上A、B 两类缸体毛坯材料性能差异与切削性能差异;通过优化缸体后端面最大铣削弧长,提出了“两刀切”走刀路径方案;分析直槽钻断刀原因,对钻削加工参数进行了优化。具体如下:#p#分页标题#e#
(1)缸体生产线上切削 A/B 两类缸体毛坯刀具寿命存在显著差异,为此开展了针对两类缸体从材料性能到切削性能的对比实验。在探究材料性能方面,从元素成分测试、观察灰铸铁金相组织、布氏硬度等方面展开了对比分析;并揭示了 A 类缸体毛坯铸造过程中元素成分不合理、金相组织不均匀、硬度波动大的现象。最后通过切削对比实验,论证了 A 类缸体材料性能较差是导致切削性能差、刀具寿命低的主要原因。
(2)通过正交实验和采集现场电流数据,分别建立随加工 A/B 两类缸体件数变化的铣削力模型。在此基础上,建立切削弧长与铣削力关系,利用 CAD lisp 语言求取走刀路径下的最大切削弧长,算出机床“闷车”阈值。基于优化加工区域最大切削弧长理论提出了“两刀切”的走刀路径方案。开展了采用两种走刀路径加工缸体时主轴电机电流对比实验,发现“两刀切”走刀路径加工状态下的主轴电机三相电流峰值均小于 SGMW 生产线上现用走刀路径,且前者电流波动情况明显优于后者,论证了该方案的有效性。
(3)通过正交实验,分别建立了直槽钻、螺旋钻加工缸体的钻削轴向力与钻削扭矩模型。在此基础上,采用极差法分析钻头直径、每转进给量、钻削速度对直槽钻、螺旋钻钻削载荷的影响程度。采用分段进给的方法分析直槽钻断刀的原因,通过对比实验得出切屑排出不畅、退刀时钻头承受的扭矩异常增大而过载是断刀的主要原因。针对直槽钻加工的特点,设置对比实验对钻削参数进行了优化。
..........
参考文献(略)