1 绪论
1.1 论文研究背景与意义
随着数据时代的到来,许多企业已经认识到,数据是企业重要的战略资产。如何从海量的数据中洞察出数据的规律,挖掘出数据的价值,提高企业综合的信息利用能力,提升数据资产的战略意义,如何将挖掘到的数据可视化,指导给企业不同层级人员分析和决策,指导企业的智能运营与生产,这些已经成为当下企业迫切的需求。在此需求的推动下,商业智能、数据分析迎来市场的新机遇、新拐点。大量的数据分析工具层出不穷,产品逐步趋于成熟与同质化,但结合目前市场主流产品,发现企业级数据分析工具仍然存在许多问题。
目前,西安西电操动机构的质量管理系统存在一些问题。传统 SPC 控制图识别异常模式、异常点的能力弱,不能指导车间质量监管人员及时地找出质量问题;系统数据冗余、数据碎片化严重、数据孤岛;系统的业务规则与逻辑代码未分离,系统难以适应复杂、多变的业务规则;数据分析和数据可视化程度低,难以探索数据潜在的价值。企业质量管理系统存在的具体问题如下:
企业目前主要采用 SPC 统计过程控制技术对制造过程中的产品进行质量分析和监控。该技术可以使质量数据以控制图的形式呈现给用户,形象地显示出产品制造过程中质量特性的波动状况,车间质量管理人员可以实时地监控产品质量的变化,若控制图出现异常,则生产过程失控。但是,该技术缺乏对控制图异常模式的智能识别。
系统数据冗余、数据碎片化严重、数据孤岛等。从数据接入、预处理、多维分析、预测分析、模型部署应用,均有不同的产品实现,分析过程因工具的不完整而造成分析链条的割裂,给客户带来了较大的学习成本与部署成本,降低了数据分析与价值应用的效率。
..........................
1.2 国内外研究现状
数据分析在制造领域起到重要作用,控制图作为制造过程的分析工具,受到广泛使用,控制图代表生产过程质量特性是否处于稳定状态,实时地发现异常控制图背后质量特性的异常原因具有重要意义。本文主要对统计过程控制(Statistical Process Control,简称 SPC)控制图模式识别做深入研究[1-6]。另外,针对传统信息系统难以满足实时变化的业务需求,采用规则引擎开发数据分析及可视化平台。因此对规则引擎做也做深入研究。
1.2.1 模式识别的研究现状
目前,制造企业大多采用 SPC 技术,对生产过程中产品的关键零部件进行质量分析和监控。该技术可以使质量数据以控制图的形式呈现,形象地显示出产品加工过程中质量特性的波动状况,根据这种波动状况,车间质量管理人员就可以实时监控加工过程产品质量的变化,以此判断整个加工过程是否处于稳定状态。若控制图出现异常,则生产过程失控,此时需要及时发现并消除潜在的质量异因,从而采取相应的措施予以纠正。
传统的 SPC 质量控制图模式又称为基本控制图模式,它以质量管理理论中的八大判异准则作为判别控制图的异常点。通过研究大量相关理论资料发现,这八大判异准则对判别控制图上的数据点异常点过于细腻,很容易出现误判的情况,将原本生产质量过程处于稳定或者受控状态的质量数据点误判为质量异常点,质量数据分析人员需要浪费大量工作时间寻找对应质量异常的原因,这往往给质量数据分析人员造成了不必要的麻烦,从而降低了产品的生产效率。因此,传统采用 SPC 质量控制图技术不能准确监控质量状况。如何根据控制图的状态模式来判断加工过程质量特性是否存在异常,这是加工过程质量控制要解决的关键问题。
.......................
2 相关理论概述
2.1 神经网络理论
人工神经网络(Artificial Natural Networks,简称 ANN)是一种处理数据的数学模型,它由许多神经元按照顺序互相连接形成的网状结构,数据借助这种具有网络结构的载体向前传播。ANN有着雄厚理论基础,许多研究者通过深入地研究和学习ANN,解决了很多实际问题,特别是解决了数学、模式识别、机械故障诊断等领域的棘手问题。
ANN 有多种分类。按照性能可以分为连续型网络、离散型网络、确定型网络和随机型网络;按照拓扑结构可以分为前向网络和反馈网络,其中前向网络有自适应线性神经网络(AdaptiveLinear,简称 Adaline)、单层感知层、多层感知层、误差反向传播算法(Error Back Propagation Training,简称 BP 网络)等。本文主要对 BP 网络做进一步研究。
2.1 神经网络理论
人工神经网络(Artificial Natural Networks,简称 ANN)是一种处理数据的数学模型,它由许多神经元按照顺序互相连接形成的网状结构,数据借助这种具有网络结构的载体向前传播。ANN有着雄厚理论基础,许多研究者通过深入地研究和学习ANN,解决了很多实际问题,特别是解决了数学、模式识别、机械故障诊断等领域的棘手问题。
ANN 有多种分类。按照性能可以分为连续型网络、离散型网络、确定型网络和随机型网络;按照拓扑结构可以分为前向网络和反馈网络,其中前向网络有自适应线性神经网络(AdaptiveLinear,简称 Adaline)、单层感知层、多层感知层、误差反向传播算法(Error Back Propagation Training,简称 BP 网络)等。本文主要对 BP 网络做进一步研究。
BP 网络是一种逼近任意非线性网络,它具有很强的映射能力。一般情况下,BP网络由输入层、隐含层和输出层三层网络组成,每层网络又由许多小神经元构成,网络的各层神经元数、隐含层数、网络的学习系数等参数可根据具体情况设定,具有很大的灵活性。因此所以它在模式识别、质量诊断等领域被广泛的应用,且成功率高。
...........................
2.2 规则引擎理论
2.2.1 规则引擎的概念
规则引擎始于基于规则的专家系统,它采用推理技术和模仿领域专家经验推理实际的业务规则。它是嵌入在应用程序中的组件,其目的是抽取应用程序中的业务规则,实现业务规则和程序代码分离。规则引擎使用人们容易理解的语义编写业务规则,规则引擎有相应的模式匹配算法,通过匹配算法匹配当前工作内存中的数据对象或者事实与加载在引擎中的业务规则,一旦匹配成功,相应的业务规则被激活,并触发应用程序中与规则对应的动作或操作。鉴于规则引擎的优势,本文将规则引擎作为推理机,将业务规则写入规则数据库中,方便用户根据业务变化自主更改或重新配置业务规则。
2.2.1 规则引擎的概念
规则引擎始于基于规则的专家系统,它采用推理技术和模仿领域专家经验推理实际的业务规则。它是嵌入在应用程序中的组件,其目的是抽取应用程序中的业务规则,实现业务规则和程序代码分离。规则引擎使用人们容易理解的语义编写业务规则,规则引擎有相应的模式匹配算法,通过匹配算法匹配当前工作内存中的数据对象或者事实与加载在引擎中的业务规则,一旦匹配成功,相应的业务规则被激活,并触发应用程序中与规则对应的动作或操作。鉴于规则引擎的优势,本文将规则引擎作为推理机,将业务规则写入规则数据库中,方便用户根据业务变化自主更改或重新配置业务规则。
为了便于理解规则引擎,下面介绍一下基于规则的专家系统。基于规则的专家系统框架如图 2-3 所示。
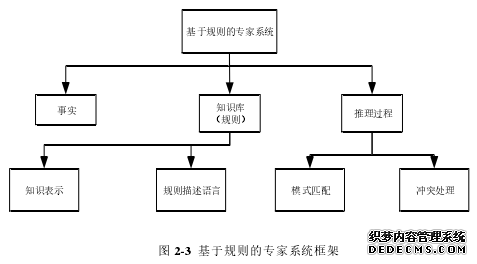
........................
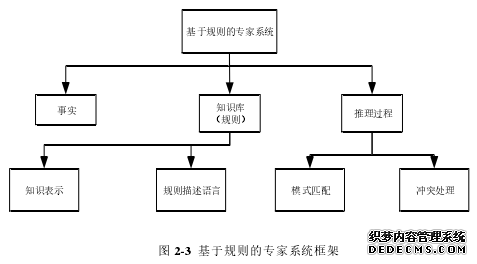
........................
3.1 制造过程质量控制图模式识别算法研究 ................................. 19
3.1.1 制造过程质量控制图模式的分类 ..................................... 20
3.1.2BP 网络结构设计 ................................................... 23
4 基于规则的数据分析与可视化系统需求分析 ............................. 31
4.1 基于规则的数据分析与可视化系统功能需求 ............................. 31
4.2 基于规则的数据分析与可视化系统用例图 ............................... 32
4.2.1 系统整体用例图 ................................................... 32
4.2.2 业务规则用例图 ................................................... 33
5 基于规则的数据分析与可视化系统设计与实现 ........................... 41
5.1 基于规则的数据分析与可视化系统功能架构 ............................. 41
5.2 基于规则的数据分析与可视化系统实现 ................................. 42
5.3 控制图模式识别算法在本系统中的应用 ................................. 49
5 基于规则的数据分析与可视化系统设计与实现
5.1 基于规则的数据分析与可视化系统功能架构
本系统由数据管理、数据分析、规则中心、算法管理、成果发布等模块构成。系统功能架构如图 5-1 所示。
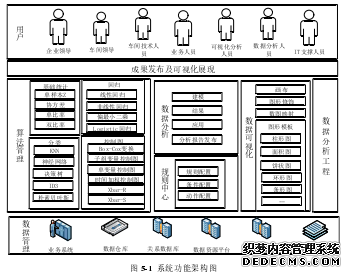
系统采用“数据看板”的形式,对数据分析结果进行集中展示,使不同质量人员通过看板可以清晰明了的看到不同层次上的质量信息;提供质量特性管理、业务规则配置、控制图分析、算法分析、异常原因处理、综合报表等多方面的功能,质量工作人员可以实时监控控制图的状态,质量主管可以总览全厂生产状况,支持计量质量特性和计数质量特性,支持大批量质量特性也支持小批量质量特性,质量特性可任意建立,不受数目、具体应用情况的限制。
........................
6 总结与展望
6.1 总结
本论文所有的研究都是以目前西安西电操动机构的质量管理系统存在的问题为出发点,研究基于 BP 的方法是解决传统 SPC 控制图识别异常模式和异常点的能力弱,不能指导车间质量监管人员及时地找出质量问题;基于规则的方法是解决传统系统的逻辑代码与业务规则的未分离而引发的系统不能适应复杂多变的业务规则的问题,主要是采用 Drools 规则引擎技术,应用 Rete 规则推理算法实现事实与规则的匹配,且规则存储在规则库中,业务分析人员可以根据业务需求自主更改业务规则,实现系统的逻辑代码与业务规则的分离。前者是数据分析的方法之一,后者在系统开发层面的方法,最终系统以后者为依据。本文取得的主要成果具体总结如下:
(1)针对传统 BP 神经网络算法进行控制图模式识别的缺陷,本文改进了 BP神经网络算法,提出一种神经网络激励函数参数可调和阈值自动调整的控制图模式识别算法,并通过蒙特卡罗法优化模拟样本,使样本数据更具与实际生产数据更接近。通过网络训练和测试,得出了识别结果,通过比较与其他模式识别算法在相同条件下识别控制图模式的结果,验证了本文算法拓扑结构更简单,收敛更快,识别速度更高。另外,对基于规则的控制图异常模式进行了推理研究。
(2)针对西安西电操动机构公司现有的质量管理系统难以适应迅速变化的业务规则。本文给出了系统功能的需求分析,采用了基于 Drools 规则引擎技术开发系统,设计并实现了系统,通过 Rete 推理算法进行业务规则与事实的匹配,让用户根据实际需求通过平台自主配置业务规则,实现了业务决策者的业务逻辑同开发者的技术逻辑分离开。
(2)针对西安西电操动机构公司现有的质量管理系统难以适应迅速变化的业务规则。本文给出了系统功能的需求分析,采用了基于 Drools 规则引擎技术开发系统,设计并实现了系统,通过 Rete 推理算法进行业务规则与事实的匹配,让用户根据实际需求通过平台自主配置业务规则,实现了业务决策者的业务逻辑同开发者的技术逻辑分离开。
(3)最后,利用本系统开展了实例应用。其中,以制造过程关键工序的质量特性为研究对象,利用本文改进的 BP 神经网络算法,结合本系统的业务规则匹配功能,实现了质量控制图异常模式的识别,并给出了相应的质量异常原因和纠正措施,验证了该算法的实际可行性和本系统的有效性、可靠性。
参考文献(略)
参考文献(略)