本文是物流管理论文,本文通过鱼骨图分析法和工业工程ECRS分析法对A车身车间入厂物流模式进行分析,提出了入厂物流模式优化方案和空箱返空模型优化方案;通过归纳总结和几何分析法,得出库存结构模型优化方案;最后通过科学的管理方法,设置供货包装优化方案和设立科学合理的考核机制。一、本文研究结论A车身车间在研究和借鉴同行入厂物流理论和实践的基础上,联系自身生产运行模式的点,入厂物流模式从物流园区逐步向工厂库模式转变,并不断优化提升入厂物流效率和降低入厂物流成本,实现A车身车间入厂物流整体方案优化。本文主要研究结论如下:第一、入厂物流模式对入厂物流成本起着关键性决定作用。入厂物流模式直接决定零部件入厂物流节点组成,对物流资源构成起决定性作用,多余的物流节点大大增加了物流运营成本。第二、单独物流功能要素的优化并非整体最优,物流方案优化需要权衡各功能要素之间的关系,寻找最佳组合方案。物流各功能要素之间普遍存在效益背反现象,一个功能要素最优可能会影响其他功能要素的实施。第三、包装标准化是入厂物流方案优化的必然选择。包装作为主机厂零部件入厂物流的起点,包装标准化不仅有助于提高其装卸搬运和返空效率,而且有助于提高运输卡车满载率和节约包装容器存储空间,降低整体运营成本。
..........
第一章绪论
A汽车厂为了实现自身零部件的零库存,以及兼顾供应商供货批量规模效益,在主机厂周边设立物流园区,物流园区由第三方物流公司进行投资建设和管理,园区内部零部件资产仍然归属零部件供应商,采用联合管理库存技术,为保障供应商权益,物流园区内部物流作业由汽车厂统一与第三方物流进行结算。物流园区根据汽车厂生产拉动情况向制造车间进行配送。这虽然降低了A汽车厂的资金占用,及实现账面上的零库存,但实质上只是将零部件库存转移给零部件供应商,并没有降低供应链总成本。由于设置物流园区中转环节,A汽车厂每年在物流园区费用支出超过6亿元。为实现工厂内部快速响应和低库存水平的目标,A汽车厂零部件由物流园区定时配送入厂,高周转的同时牺牲了卡车有效装载率,A汽车厂当前平均卡车装载率为55.5%,远低于丰田等汽车制造厂平均85%装载率的水平,大大增加了物流运营成本。
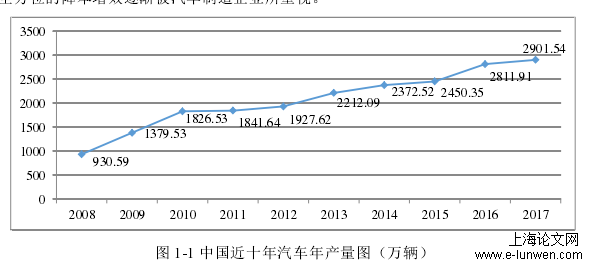
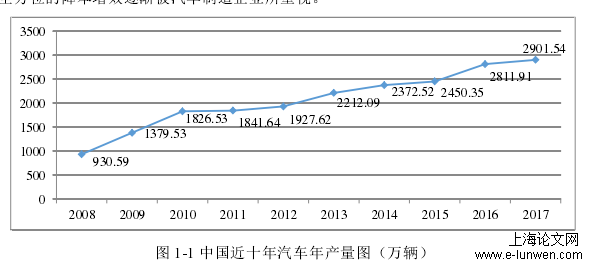
.......
第二章A车身车间及其入厂物流介绍
2.1A车身车间及其主要物流流程介绍
针对大外购零件,卡车到达卸货雨棚打开飞翼后,卸货叉车司机将零件叉到入库检验区,物料工检验并扫描入库完毕,入库叉车司机根据车载PC将零件叉到车间内部物流区相应的库位进行存储。在接收到生产线零件要货需求之后,备货叉车司机将零件叉到对应的上线站点(出库准备区),然后上线牵引车司机将满箱零件送至生产线旁,进行线旁空满交换,并将空箱带回上线站点,备货叉车司机将空箱叉回空箱整理区,入库叉车司机从空箱区将空箱叉到卸货雨棚底下,卸货叉车司机将空箱装上卡车。对于小外购零件,卡车到达卸货雨棚打开飞翼后,卸货叉车司机将存放着小外购零件的转运车卸到入库检验区,等待检验入库后,牵引车司机带着转运车将零件投递到相应的多层料架上,备货人员根据生产线零件要货需求进行备货,并将零件存放到上线转运车上面,上线牵引车司机带着满箱将零件投递到线旁的精益料架上,并将空箱返回到转运车上存放,最后将承载空箱的转运车返回上线站点,入库人员将承载空箱的转运车返回雨棚底下等待卡车返空。
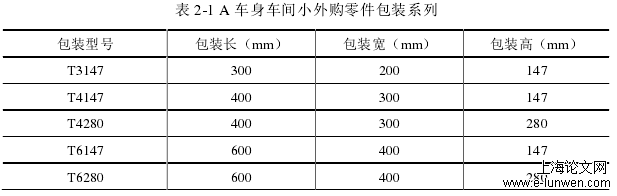
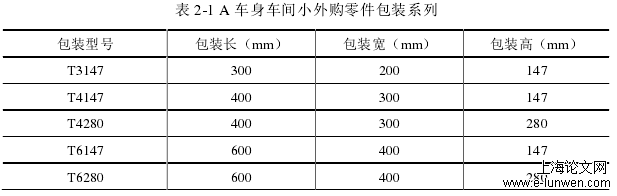
2.2A汽车厂入厂物流模式介绍
主机厂将零件的生产需求,以看板拉动的形式发送到供应商,后者组织备货,并自行安排按时将零件送至主机厂。由于主机厂存储面积有限,对供应商单次供货量进行限制,只有供货量大、满载率高以及供货量集中的供应商可以通过直送实现经济批量供货。当前A车身车间并没有直送物流模式,主要受限于车间内部物流面积不足,但在大批量物流环境下,直送物流模式最为经济。在配送中心模式基础上,分散的中转库无法实现资源上的整合,为降低供应链物流成本,打造集约型供应体系,A汽车制造厂主导设置物流园区,联合管理供应商非直送主机厂零部件。物流园区毗邻A汽车制造厂,物流园区承接供应商经济批量运输需求和主机厂小批量多批次供货需求。零部件在物流园区采用联合管理库存(JointlyManagedInventory,JMI)技术,零件管理由主机厂统一委托第三方物流公司管理,但零件资产仍然归属零部件供应商所有。
.......
第三章A车身车间入厂物流优化潜力分析..20
3.1入厂物流成本影响因素分析..........20
3.1入厂物流成本影响因素分析..........20
3.2A车身车间入厂物流成本分析.......24
3.3A车身车间入厂物流潜在问题分析......26
第四章A车身车间入厂物流方案优化...30
4.1A车身车间入厂物流优化设计方向......30
4.2A车身车间入厂物流优化方案设计......32
4.3本章小结.......41
第五章A车身车间入厂物流优化实施保障措施与预期效果.........42
5.1A车身车间入厂物流优化方案执行保障.................................42
5.2A车身车间入厂物流优化方案预期实施效果.........................43
5.3本章小结.......46
......
第五章A车身车间入厂物流优化实施保障措施与预期效果
5.1A车身车间入厂物流优化方案执行保障
A车身车间入厂优化是在供应链管理背景下,使汽车制造厂从供应链总成本的角度探索适合自身企业发展需要的最佳入厂物流方案,这需要主机厂物流人员意识观念的变更,不再局限于主机厂内部物流方案最优,要联合供应链主要参与者设立最佳供应物流模型,建立互利共赢的合作伙伴关系,同时,项目的实施需要建立跨部门的组织机构进行联合实施。对于第三方物流公司,汽车制造企业需要帮忙第三方物流公司避免成为简单的劳务输出组织。第三方物流公司只有提供更具竞争力和更高水平的服务,成为高水平物流服务提供商,才能与主机厂强强联合,降本增效。第三方物流公司不断强化与A汽车制造厂的合作,从最开始的劳务输出,到物流设施设备服务出租,再到部分方案综合提供商。第三方物流公司综合能力不断得到加强,A汽车制造厂物流服务成本也得以不断降低。
5.2A车身车间入厂物流优化方案预期实施效果
A车身车间入厂物流模式的优化涉及物流要素的各个环节,只有当各环节在相互权衡中取得更低总物流成本,才能实现优化的目的。本文通过第三章对A车身车间入厂物流优化潜力的分析以及第四章对A车身车间入厂物流优化方案的设计,历时两年,在工厂内部扩建车身车间物流工厂库11250㎡和实施优化方案,预计最终可实现单车入厂物流成本降低85.85元,A汽车制造厂年产30万辆预计每年可降低总物流成本约2575.5万元。如图4-2所示,A车身车间每天经过供应商配送中心中转再通过物流园区中转配送,或者日供货量较大但仍然通过物流园区中转配送的物流量之和占比高达43.27%,日均送货物流量929.5m³,通过改变返空模式和增加车间内部物流面积,此部分零件直接与A车身车间进行空满交换,无需经过物流园区中转,按照A车身车间入厂供货卡车平均满载率55%计算,由此每天可节约供货物流园区供货卡车36.3趟。此外,零部件不经过物流园区中转,物流相对应的零部件卸货、检验、入库、出库拣货、装车等环节将不复存在,对应的人员和工艺车辆将可同步调整。
........
结论
值得注意的是,本文第3章和第4章通过分析得出物流园区入厂物流模式成本较高,但这是建立在成熟稳定的市场份额基础上计算得出,对于刚起步、市场不确定较大的汽车制造厂而言,自建更大的物流空间则意味着主机厂需要承担更大的投资风险。汽车零部件入厂物流是一项复杂的系统工程,需要从更加严谨、科学的角度进行系统性思考和规划,并结合不同的实际场景进行不断的优化。未来A车身车间入厂物流还需要从下面两个方面加以深入研究:第一、采用推拉结合的零部件供货模式。物流缓存向生产线供货采用拉动式供货方式,供应商向车身车间供货根据生产计划信息采用推动式供货方案,在车间内工厂物流确保线旁操作先进先出以及人机工程需求,在车间外入厂物流确保零部件备货、运输、入库等综合物流成本最低。第二、降低必要生产柔性。减少质量缺陷、供货不及时、设备故障等非市场需求因素导致的生产波动,减少入厂物流必要的作业环节,在价值链上游、物流管理运作之前控制成本的产生。
参考文献(略)