本文是一篇硕士论文,硕士论文是硕士研究生所撰写的学术论文,具有一定的理论深度和更高的学术水平,更加强调作者思想观点的独创性,以及研究成果应具备更强的实用价值和更高的科学价值。共分为12大类。(以上内容来自百度百科)今天为大家推荐一篇硕士论文,供大家参考。
引 言
钢铁工业是国家的支柱工业。在过去的几十年里,钢铁工业有了长足的发展,2017 年全年,全国粗钢产量 8.32 吨亿吨,同比增长 5.7%;生铁产量 7.1 亿吨,同比增长 1.8%[1];然而,钢铁工业属高能耗工业,占全球总能耗的 4~5%。此外,钢铁工业对环境也具有十分严重的影响,据估计,吨钢所产生的温室气体 CO2约为1.88 吨。根据世界钢铁协会和中国钢铁企业网给出的统计数据,中国吨钢耗能为1.755GJ,这相当于 4.937 亿吨标煤,所产生的 CO2为 15.642 亿吨。目前,在节能减排的紧迫需求下,回收钢铁生产过程中所产生的余热是有效的手段之一。因此,针对钢铁工业,世界范围内的研究人员积极开发多样的余热回收技术。高炉渣是钢铁行业富含热能最大的副产品,每吨液态熔渣蕴含热量相当于60kg 标准煤所产生的热量[2],目前行业吨铁渣量在 350kg 左右;按照 2016 年全国生铁产量 7.07 亿吨计算,全年生产高炉渣 2.47 亿吨,蕴含热量相当于 1485 万吨标准煤;因此高炉渣热能回收利用前景广阔。面对传统高炉水冲渣工艺具有水资源浪费严重、SO2等有害气体排放量大、过程热量回收困难等因素,深入开展高温熔渣的无水离心粒化工艺技术,是提高有效热能回收和降低有害气体排放的主要方向。高炉渣余热回收工艺技术研究,得到国内外学者和科研机构的重视,但是其余热回收和利用仍然处于较低水平。目前,高炉渣热能的利用还仅限于冲渣水余热供暖,但是在长江以南,无需供暖的地区,其热能利用率更低,不仅增设的冲渣水冷却设施电能消耗较大,而且会消耗大量的水,造成环境污染。因此,对高炉渣的热能的回收利用显得非常重要。高炉渣余热回收对环境保护和生产成本的降低都具有重要的实际意义。
本文对国内外高炉渣的水淬处理工艺和干法处理工艺进行了总结,并对高温熔体的构成进行科学假设,以独立的粒化渣颗粒为研究单元,分析了粒化渣颗粒在各种外力交互作用情况下的粒化和其自身的相变规律,结合数值模拟结果,明确了制约机械离心粒化系统间歇性运行的关键因素,并通过实验研究探索出一整套关键控制参数;在后续的关键技术研究试验中,进一步验证了工艺优化后的机械离心粒化系统,使之能够与高炉的生产节奏相匹配,实现液态炉渣离心粒化系统运行的持续性,使高炉渣热能的持续回收成为可能。
........
第 1 章 绪论
1.1 课题研究背景和意义
1.1.1 课题来源
本课题研究是仪垂杰教授主持的国家自然科学基金重点项目《高温异质离散运动颗粒间传热传质机理研究》(50934010)的一部分,是基于青岛理工大学已故特聘院士姚福生提出的“利用高炉渣余热裂解生物质制取生物质油”的研究计划,并通过“冶金炉渣高效资源化利用国家地方联合工程研究中心”,经过数年时间的研究和探索,所取得的成果。
1.1.2 机械离心粒化机理研究的意义
(1)传统高炉渣的水淬工艺弊端
在百年钢铁历史中,高炉渣水淬工艺成为高温液体熔渣处理技术的主流;在熔渣水淬过程中,大量的水资源消耗、无序排放的 SO2气体以及大量的熔渣显热被浪费。传统的高炉渣水淬工艺和水渣处理过程中,在熔渣水淬的瞬间,高温熔渣的热能被浪费,以水蒸气的形式排放的大气中去,每吨渣消耗约 1 吨水,同时生产大量的 SO2和 H2S 等有害气体,即使环保型 INBA 渣处理工艺也无法克服这一缺陷[3]。高温熔渣水淬工艺生产的水渣含水量在 18%左右,钢铁企业自备微粉加工车间的情况下,水渣含水量越高,工序能耗越高,加工成本也就越大。高炉熔渣的温度可达到 1450~1520℃,因而熔融态高炉渣的总能量相当于 1100万吨标煤所含的热量(每吨高炉熔渣所含热量约为 1.26~1.88×106KJ)[4],这相当于高炉过程总能耗的 13.0%。
........
1.2 传统高炉渣处理工艺进展
1.2.1 水淬法高炉渣处理工艺
在高炉炼铁的历史中,尤其是现代化的高炉生产组织,水冲渣依然是最简洁、高效的处理方式,且不断进步;目前传统的高炉渣处理工艺[5]主要有:拉萨法(RASA)、图拉法(TYNA)、明特法(MTC)、底滤法(OCP)、因巴法(INBA)。拉萨法渣处理工艺是英国 RASA 公司和日本钢管公司联合研发的;并于 1967年首次应用于在日本福山钢铁 1 号高炉(2000m3)。上海宝钢是中国第一个应用拉萨法的钢铁企业,技术引进来自于日本,见图 1-1。相比其他水冲渣工艺,拉萨法的最大优点是水资源利用率高。高炉熔渣在冲制箱被水淬制成水渣,进入粗分槽;渣水混合物由渣浆泵送至脱水槽,脱水后的水渣可以直接汽车运走,槽中的浊水流入沉降槽;在沉降槽内,在底部由渣浆泵把沉降的渣水混合物再次打入脱水槽,槽中的水流入温水槽,随后由渣浆泵送至冷却塔,返回炉前进行再次冲渣作业,用于水淬高温熔渣;如此,完成一个闭路循环,达到水资源循环利用的目的。图拉法也是目前非常成熟的高炉渣处理工艺见图 1-2,它第一次应用在俄罗斯图拉厂 2000m3的高炉上。1998 年首钢 2560m3首次引进了三套图拉法处理装置,至今运行良好;2004 年青钢新建两座 500m3高炉,也引入了图拉法渣处理工艺,占地小、操作灵活。
.......
第 3 章 熔渣粒化过程中流动传热规律与熔渣中液固相变演化规律研究....37
3.1 熔渣未离开粒化盘时的流动、传热规律研究..............37
3.2 熔渣颗粒化初始阶段时的流动与传热过程的规律研究.........44
3.3 单个渣颗粒物相演化模拟.............49
3.4 本章小结.........61
第 4 章 高炉渣机械离心粒化优化实验研究......63
4.1 高炉渣自身性能对离心粒化工艺影响规律的研究....63
4.2 高炉渣离心粒化实验平台的搭建..........71
4.3 高炉渣机械离心粒化实验结果及分析.............79
4.4 本章小结........82
第 5 章 高炉渣机械离心粒化关键技术研究........85
5.1 高炉渣机械离心粒化关键技术研究的理论基础...........85
5.2 高温液态熔渣离心粒化试验研究基础.....85
5.3 高炉渣机械离心粒化关键技术研究思路............86
5.4 高炉渣机械离心粒化关键技术研究实施过程....90
5.5 高温液态熔渣离心粒化试验结果分析....94
5.6 高温熔渣离心粒化关键技术研究实施过程中取得的创造性成果..............112
5.7 本章小结.......119
第 5 章 高炉渣机械离心粒化关键技术研究
5.1 高炉渣机械离心粒化关键技术的理论基础
基于实验室离心粒化试验,熔融态的高炉渣落到电机带动而高速旋转的粒化盘上后,在重力的作用下,由柱状渣流变为平铺状液态熔渣,高温液态熔渣与粒化盘之间形成具有一定厚度的渣壳,渣壳与液态熔渣之间没有明确的界面;熔渣在固态渣壳的带动下,作圆周运动的同时,在离心力和黏滞力的共同作用下,快速减薄,形成渣膜,并逐渐向着粒化盘的边缘运动。抵达粒化盘边缘后的渣膜按照波理论破裂成丝,沿粒化盘圆周切线方向飞离,并断裂,在表面张力的作用下,收缩成球状颗粒。在随后的高温液滴飞行过程中,被迅速风淬冷却至黏结性温度点,触壁反弹后,被收集在一起,进入随后的换热系统。其过程存在辐射换热和对流换热两种形式,热量被即时带走,保持粒化装置内的低温环境,强化了离心粒化过程的风淬效果。根据实验研究结果:在1450-1550℃的温度条件下,三种不同直径的粒化盘,分别按照900r/min、1400r/min、1900r/min、2400r/min的转速进行对比试验;并重点对直径200mm的粒化盘,在1900 r/min的转速进行上下调节,发现转速在1750r/min时,离心粒化效果最好。通过实验研究,不仅验证了高炉渣离心粒化机理,而且验证了解决机械离心粒化可持续性及余热高效回收的关键问题;明确了影响高炉渣离心粒化技术的合理参数,获得离心粒化调控规律。粒化盘的转速和直径直接决定了离开粒化盘边缘的瞬间,熔滴所具备的动能;在粒化盘边缘构成渣膜的熔渣液滴获得的动能大于表面张力带来的势能,才能顺利完成离心粒化过程。
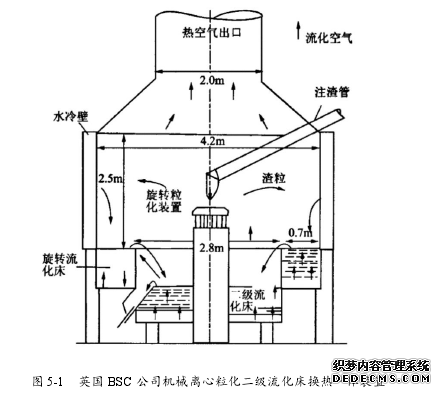
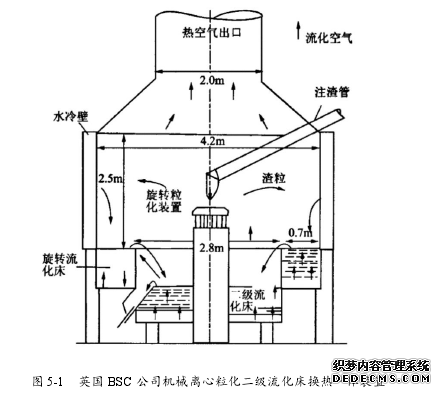
......
结论
本文以高温液态熔渣的机械离心粒化及余热回收系统为研究对象,对高温液态熔渣的离心粒化及液固相变演化理论进行了研究,建立了高温液态熔渣的离心粒化数学模型和液固相变演化数学模型,开发了有利于高温液态熔渣可持续离心粒化的新型二级换热及热回收系统,并通过数值模拟分析从理论上证明了机械离心粒化的可行性。基于结果及单颗粒炉渣运动模型分析,建立了高温液态熔渣机械离心粒化的实验室平台,并以实验研究为基础,在钢铁厂现场进行了放大关键技术研究,在关键技术研究过程中,通过一系列技术创新和工艺改进,解决了粒化渣颗粒沾结粒化装置内壁和颗粒间互相黏连的难题,建立了高温液态熔渣离心粒化与余热回收一体的二级换热系统,实现了工艺创新与节能创新的技术进步;并通过关键技术研究进行了热回收量的初步核定。通过开展理论分析、数值模拟、实验室及关键技术研究试验研究,得出以下结论:
(1)运用波理论相对准确地分析液态熔渣在粒化盘上减薄、成膜的运动过程,阐明了渣膜破碎、成丝、断裂、收缩成球的粒化机理;
(2)通过液态熔渣的相变演化理论,得出相变演化问题主要包括相间物理转化和过程传热两个物理过程。相变过程传热方式主要有三种,分别是:液态渣滴冷却过程的气液对流传热、渣粒内部液固相变演化过程的潜热释放传热、固态渣粒冷却阶段的气固对流传热。
(3)表面张力是影响粒化渣颗粒尺寸的主要原因,表面张力越小,越有利于形成细小、均匀的粒化渣颗粒,保持较高的初渣温度,有利于离心粒化;随着初渣温度的降低,表面张力增大,合理转速将增加,才能达到理想的粒化效果。
(4)通过数值模拟分析可知,单个渣粒在飞行过程中的液固相变演化过程,受粒径、相对风速、环境温度的影响程度最大;在实际操作过程中,控制各因素的影响来减小粒径、提高相对风速、降低环境温度,以得到高玻璃化率的渣产品,并同时保证粒化过程的可持续进行。
..........
参考文献(略)