本文是一篇工程管理论文,工程管理就是对工程或者说工程建设进行管理,这里的工程指的是指土木建筑工程。工程管理是对一个工程从概念设想到正式运营的全过程(具体工作包括:投资机会研究、初步可行性研究、最终可行性研究、勘察设计、招标、采购、施工、试运行等)进行管理。(以上内容来自百度百科)今天为大家推荐一篇工程管理论文,供大家参考。
第 1 章 绪论
1.1 选题背景和意义
随着越来越激烈的全球商业竞争,企业都在寻找各种方法来赢得对竞争对手的竞争优势,随之增长的用工成本和快速变化的市场需求更增加了企业的生存压力,对于生产制造企业来说,如何降低成本,提高效率,缩短生产周期成为企业在激烈的商业竞争中生存与发展的急迫需要解决的问题。精益生产作为一种行之有效的管理方式[1],自从被沃麦克和琼斯等人总结推广以来,不断地被各行各业所接受,并不断发展。从理论的角度看,虽然丰田生产方式被总结成精益生产理论已经有二十多年的时间,但是精益生产方式及精益思想被正式引进中国只不过十多年时间。因为精益生产涵盖面广,关乎企业的每个职能部门,涉及企业经营的各个环节,并且各方面环环相扣于整个价值链,导致公司员工甚至部分中层管理者在生产过程缺乏全局观念、理解片面、本位主义等问题。因此,在精益生产管理基本框架内,如何寻找适合的更接近操作层面的理论和实践方法,对于多品种小批量的制造型企业而言更是一个难题。本文选取 V 公司为研究对象,其所在的造纸设备行业是典型的多品种小批量的行业,研究精益生产理论在 V 公司的实践活动,其通过精益生产理论的实践,不断发现问题,消除浪费,降低成本,缩短交期,提高企业综合竞争力,为公司实现长期稳定的发展奠定基础。通过这些成功案例的研究和分析,给类似的多品种小批量推行精益生产提供一些参照和借鉴。
...........
1.2 国内外研究现状
1、国外的研究现状
精益生产理论在日本丰田生产方式(TPS)的基础上发展而来,在日本的汽车企业取得了巨大的成功后,日本的精工电子,家电,制造等行业相继引入了精益生产方式,并取得很大成功。后来,精益生产的思想逐渐被如钢铁,炼化等流程制造业接受,创造出适合不同行业特点的管理思想。目前精益生产的思想在日本正在被零售,航空服务等非制造的产业吸收和应用,如很多零售商业,准确分析顾客的购买需求,实时的快速补货,从而达到优化库存,避免货架缺货,满足顾客需求的目的。欧美等国家在上世纪八十年代就掀起了学习精益生产的热潮,特别是美国在总结丰田 TPS 系统的基础上提出了精益生产的理论。在美国的企业推广,并结合其自身信息技术产业的优势,创造性地将精益的许多思想及工具应用到 ERP 系统中。后来,又提出敏捷制造,流程重组,建立学习型组织等理论结合精益生产的理论应用于企业,使精益生产的理论更符合其本国特色。美国的 GE 公司[]在其制造业部门实施精益生产取得成功后,大力推动将精益思想导入到非制造业,大大提高了金融服务等行业的效率。
..........
第 2 章 精益生产理论概述
2.1 精益生产的基本理论和原则
精益其英文为 Lean, Lean 在英文里是指“没有赘肉且结实”的意思,引用到企业的经营活动上,是要将一家企业运营成没有任何资源浪费的现象,运作成精致且结实的样子,并可持续发展[2]。“精”就是在产品生产制造的每个流程上,在产品品质上追求精益求精;“益”就是通过追求精益求精,消除各种浪费,以最小的投入实现最大的产出,从而使企业利润达到最大化[3]。精益生产是提高企业活力的一整套概念和方法的体系,基本思想是“消除浪费”,通过对整个生产流程的优化,让产品生产制造的每个环节更合理同时控制好品质,实现总成本节约。理论源于实践,服务于实践,在实践中被不断验证并丰富和提升。精益生产理论是新技术的发展和新管理思想紧密结合的产物。在 1985 年,美国麻省理工学院筹集 500 万美元,组织了多位行业专家,花费 5 年的时间对 15个国家的 90 多家汽车公司进行考察,并比较分析了大量公开发表的相关资料,充分而全面的比较分析了以福特为代表的大批量生产方式和以丰田为代表的小批量,多品种生产方式,提出了精益生产的概念。在精益生产发展的过程中,不同学者对其的内涵和定义有如下理解。1990 年詹姆斯 P.沃麦克 (James P.Womack) 和丹尼尔 T.琼斯 (DanielT.Jones)出版了《改变世界的机器》一书在总结丰田生产方式的基础上,更加关注从产品研发,销售和生产的全流程,并将其定义为“精益生产”,并进一步说“精益生产方式”是“精益”的。麻省理工学院这样定义精益“确切的说,丰田生产方式就是精益生产方式,是一种不做无用功的精干型生产系统”[4]。
.........
2.2 精益生产实践的工具
上面我们阐述了精益的 5 项原则,这些原则在将一个传统的生产管理转化为精益生产管理的实践活动中都能体现出来, 这些实践活动包含:客户的需求分析; 价值流分析;减少/消除浪费; 工作场所和系统的优化;牢固和高效的关系网;生产客户需要的产品;问题发现和解决。当然这些实践活动都依赖一些工具和技术来实现。这些工具和技术是是实施精益的有效路径。我们广泛使用和知道的工具和方法有:准时生产制(JIT);快速换模(SMED);看板/拉式生产;标准化;5S;价值流成图(VSM);供应商参与/整合;根本原因分析(5Why);全员参与;可视化管理;客户参与;PDCA 循环等等;在实践精益原则时,很多工具的实施是相互依赖的,有些工具在实施前需要先实施一些其他的工具,所以在选择先使用哪些工具和技术要是情况而定,更多的是取决于实用性和经济性。
.........
第 3 章 V 公司组装车间管理现状和问题分析 .........18
3.1 V 公司组装车间介绍.......18
3.1.1 V 公司情况介绍 ....18
3.1.2 V 公司组装车间介绍 ........19
3.2 V 公司组装车间的问题分析 ........19
3.3 V 公司推行精益生产的的可行性分析 ........23
3.3.1 组装车间改善需求分析 ......23
3.3.2 推行精益生产的策略和技术体系 ......24
3.4 本章小结.........26
第 4 章 V 公司组装车间的精益实践 .........27
4.1 V 公司精益生产管理体系-卓越运营(OPEX)体系介绍 .........27
4.2 V 公司组装车间精益实践 ..........29
4.3 本章小结.........47
第 5 章 总结和展望 .......48
5.1 V 公司精益生产实施经验和效果总结 ........48
5.2 V 公司精益生产模式仍存在的问题 ..........50
5.3 展望.....51
第 4 章 V 公司组装车间的精益实践
4.1 V 公司精益生产管理体系-卓越运营(OPEX)体系介绍
V 公司高层在市场调研和内部问题分析的基础上确定实施精益生产的管理思路,聘请了专业的精益专家组建了精益实施团队,结合公司的实际情况提出适合 V 公司的精益生产管理体系-卓越运营(OPEX)体系:可以通过下面图 4-1(卓越运营)来看一下 V 公司实现精益生产的路径:针对以上的主要问题,经过认真分析以及与现场员工探讨,按照 5S 的要求采取了以下改善措施:1)对组装区域的办公用品和工具柜按照 5S 管理的要求进行整理和整顿,整理出需要和不需要的用品,需要的用品定点摆放,不需要的用品及时清理出工作区域。对暂时不确定是否用到的用品进行标识,统计使用频次,再进行决定是否保存在装配区域。通过整理整顿将长期累积的装配图纸,长期不用的工装夹具,破损的吊带和装配工具清理出装配区域。2)针对组装区域内办公用品,工具柜和物料存放区域进行重新规划定位:划定专门办公区域给订单计划部门转移来的组装计划,工单,图纸信息;添置移动小车将常用的组装工具在移动小车上固定位置便于装配时频繁和快速拿取,减少往返和寻找的时间;对物流部门转运过来的物料按照装配产品的特点划定存放区域,以方便吊装移动为原则,减少移动距离既提高效率也能减少部件受损的情况发生。
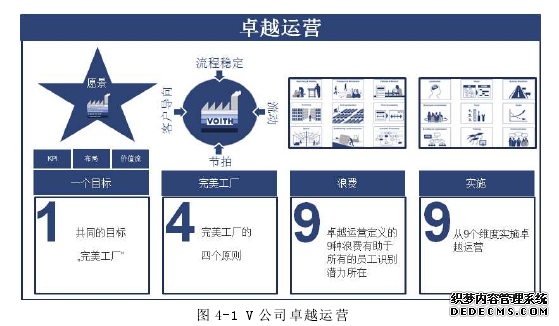
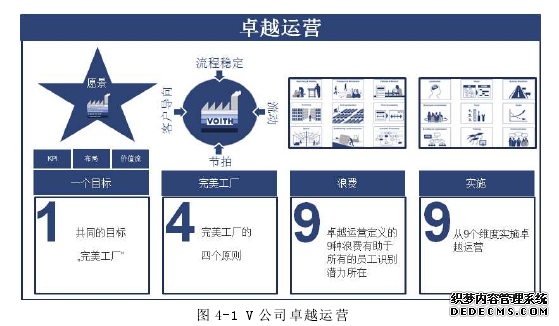
...............
总结
我们都知道精益生产活动在我们这种多品种小批量行业推行的难度,但是 V 公司结合自身特点提出的卓越运营的理念能过坚持 4 年并逐步取得效果的经验有:#p#分页标题#e#
1、公司高层的支持和参与: 精益生产活动是一种自上而下的管理活动,要求高层领导们亲自参与现场的管理和改善活动,如果领导层不参与其中是不可能取得这样的成绩。管理层在精益生产实践过程中不断展现精益领导力,带动全员一起持续改善。精益专家在车间指导现场员工运用不同的精益实践工具改善特定的工作区域。两个维度同步推进确保精益活动推行中能够相互作用,最终实现整个公司全局的改善。
2、精益理念的宣传和沟通: 公司将精益生产的理念和建设理想工厂的愿景相结合,在各种场合进行宣传,并组建专门的精益生产团队安排全员培训,让精益理念成为一种习惯一种思维方式。
3、精益实践的实际应用: 公司通过精益实践活动在车间不同区域的应用取得的成绩进行实例推广,让车间员工真切实际地体会到推行精益生产活动能够带来成效,让工作变得很顺畅。
..........
参考文献(略)