本文是一篇工程硕士论文,工程硕士论文是指工程师硕士论文,工程管理硕士论文与工程硕士论文发表的工程论文。工程硕士论文涵盖集建筑、结构、电气、暖通空调、水利、园林、市政、路桥、给排水、装修、施工、造价、节能、监理、房地产、环保、规划、岩土、林业,工程师,软件工程,工程硕士,林业工程师,电力工程, 化工工程, 控制工程,工业工程, 系统工程, 电气工程, 水利工程,工程师职称,公路工程,软件工程, 建筑工程,土木工程,工程类杂志 咨询、考试、其他等共42个类别的专业。(以上内容来自百度百科)今天为大家推荐一篇工程硕士论文,供大家参考。
第 1 章 绪论
1.1 课题研究的目的及意义
我国的工业机器人在2011年的销量只有700台,但到2016年就增长至7.3万台,7年间销售量增速100倍,年均销售量增速迅猛[1],我国对工业机器人的需求量是巨大的,工业机器人的市场应用前景是不可估量的。目前我国已经是全世界第一大工业机器人产销国。2017年,美的收购库卡提升了我国在工业机器人和自动化生产领域保持的技术优势,有利于我国机器人产业走向世界。“十三五”期间,我国我国的产业政策继续支持精密装备制造领域、服务领域和重工业产业的创新改造升级,加速我国从制造业大国向制造业强国转变。机器人产业将会遍布诸多行业,代替大量人工,大大提高生产效率, 降低生产成本。我国将不断提升自主品牌机器人研究和关键零部件的生产创新能力、推进工业型机器人和服务型机器人在相关领域的应用。一般来说,工业机器人根据其功能和需求,其外观造型要求既有简单单一的板材组装而成,也有造型富有个性且由复杂的自由曲面的零部件组成。正向设计通常是根据客户的现实需要,在大量数据积累和理论研究的基础上,借助手工绘图或 3D 设计软件完成产品的绘制,生成产品图纸,再进行零部件制造这样的生产流程[2]。但是,对于复杂曲面的产品,在我国机器人行业刚刚起步,设计经验和理论研究相对欠缺的情况下,正向设计的条件不够成熟,直接采取正向设计会导致成本增加、项目周期延长、反复修改甚至设计失败[3]。这不论从企业品牌树立、研发成本和满足客户要求等方面,都是不利的。从零部件样品—产品的逆向扫描—CAD 模型重构—产品制造,这是一种新型产品开发模式[4]。这种产品开发的特点是将已有的产品样件通过三维扫描仪器的扫描环节将产品模型转化为某软件可以识别和接受的原始点云数据,然后利用CAD 软件复原产品的 3D 模型进行创新优化再设计,借助 3D 打印或数控机床完成产品的加工制造。逆向设计通常是根据原有的样件模型通过扫描和造型等一系列方法对原产品进行复原或在此基础上对原产品进行分析、修改并进行创新优化设计,最终目的是使其产品达到原来产品的性能或者超越原有产品性能[5-6]。
..........
1.2 曲面数字化测量分类
高效、准确地实现腕关节外观表面点云数据采集是所有具有复杂曲面产品能够进行建模、评价和制造的基础[9],是实现逆向工程技术首要环节和关键,点云数据的好坏接影响到逆向工程整项工作的效率和质量。根据扫描设备的测头与被测产品表面是否接触,分为接触式与非接触式两种测量方法[11]。前者主要是通过三坐标测量仪上的传感测头(在许可行程范围内)去探测零部件的内外表面,进而得到想要的数据坐标点[12]。此测量手段测得点数据比较准确,但测量时间较长,效率较低。非接触式测量主要是通过扫描仪不直接接触被测物体,通过光线测得产品表面的点云数据[13]。这种方法测量速度快、时间短、效率高、无需探针测头的半径补偿[14],因此应用广泛。两种测量方法具体的分类如图 1.2 所示。根据工业机器人腕关节零件的特点,同时结合腕关节产品外观表面获取数据的测量精度、采集速度、产品本身曲面的复杂性、经济效益等方面,非接触式测量比接触式测量获取数据更快[15],在较短时间内采集的点云数据用足以构建腕关节曲面特征,同时无需做半径补偿。德州职业技术学院有瑞康扫描仪和泰西三坐标测量仪,依据综合性价比选用非接触式测量法来实现工业机器人腕关节曲面零件的数据采集。
..........
第 2 章腕关节样件扫描逆向建模
2.1 腕关节样件点云数据采集
点云数据采集在整个逆向工程过程中是最重要环节之一,点云数据质量的好坏关系到后续腕关节零件建模的精度和质量[45],本节选用瑞康扫描仪完成点云数据采集。
2.1.1 扫描仪镜头校准
扫描仪通过2D成角拍照方式获得点云数据[46],如果移动位置或进行重新拆装,光栅和相机的位移和角度就会发生变化。使用前,校准工作是必要的。校准完成后,相机、镜头和光栅镜不再调整。把校准板放置在扫描仪前方,确定扫描距离。精睿系列三维扫描仪最近距离可调节至25cm。依据腕关节零部件样件的大小、精细度我们将距离设置为60cm,如图2.1所示。两只相机的曝光延时时间,选用33.3333毫秒。标识点粘贴选取在平坦面或者曲率变化不大的曲面上,公共标识点至少为3个,每个摄像头度少捕捉到4个相同的标记点,进行匹配。扫描完成后对获取的点云数据依据标记点进行校准。转动腕关节零件,进行下一次扫描,直到整个被扫描物的数据获取完成。粘贴标识点要保证扫描策略的顺利实施,根据关节零件的长、宽、高合理分布粘贴。如图2.5所示标识点的粘贴较为合理。
..........
2.2 腕关节点云数据处理
将扫描的点云数据进行简单处理,删除噪声点、完成点云数据拼接、对点云数据重新取样,生成一个新的整体的腕关节点云数据,并进行数据导出[47],再用Geomagic Wrap软件进一步处理点云数据,最终完成腕关节点云数据封装。扫描获取贴有标记点的腕关节点云数据后,在进行数据处理时需要选择通过获取的标记点对扫描数据进行对齐,若数据对齐失败,则可以通过根据几何图形对齐选项对数据进行对齐后。将多个网格数据拼接成一个网格数据进行合并,再创建一个新的点云数据,删除原有数据,重新取样后调节合并后的数据点密度,对所需数据的质量进行调节。通过3D扫描仪获取数据后需要将数据需导入到Geomagic Wrap软件中对数据做进一步的处理。FlexScan3D软件支持导出的格式有如下几种:3d3、stl、obj、ply、asc、raw、png、dep[49]等格式,将腕关节点云数据导出stl格式的文件。
.........
第 3 章腕关节加工中心铣削精度分布实验研究.......... 49
3.1 基于 Powermill 的工业机器人腕关节曲面数控自动编程...........49
3.1.1 腕关节圆柱形底部编程.....51
3.1.2 腕关节主身曲面编程加工..........53
3.1.3 后置处理...........58
3.2 实验项目与实验装置.......61
3.2.1 加工实验方案设计....61
3.2.2 腕关节零部件主身面曲面偏差检测实验方案设计......63
3.2.3 腕关节表面质量检测实验方案设计............64
3.3 本章小结........65
第 4 章 腕关节零部件切削步距参数化实验结果分析.........67
4.1 确定优化参数..........67
4.2 腕关节零部件加工部位及加工使用刀具..........67
4.3 侧向步距对切削实验影响.......68
4.4 本章小结........71
第 5 章 结论与展望............73
5.1 结论.......73
5.2 展望.......74
第 4 章 腕关节零部件切削步距参数化实验结果分析
4.1 确定优化参数
腕关节零部件主身面精加工所采用加工策略是旋转面精加工,采用的方法是直线拟合逼近曲线法,加工过程中小直线段逼近法的步距对加工的影响较大[64],通过不同步距的切削实验比较三种不同方式构建的模型进行比对,评价出最优的曲面模型构建方法,切削步距主要影响的参数有加工精度、加工后零件部表面质量和加工时间,切削优化实验也主要根据这三个方面进行比对。下面对三组不同构建方式得到的腕关节主身面模型进行切削实验,毛坯选用为6061号铝合金材质。本次实验的主要目的是验证切削步距对不同构建方式下获得的腕关节零部件加工效果的影响大小,选取直径为φ8的铝合金涂层球头铣刀做精加工,并设定合理的切削参数。腕关节零部件主身面加工过程中通过加工测量表面粗糙度和精加工侧向步距的关系如图4.2所示。其中模型A为借助普通游标卡尺及千分尺测量尺寸构建的腕关节模型加工实验结果,模型B为扫描正向建模构建的腕关节零部件主身面加工实验结果,模型C为快速拟合构建的腕关节零部件主身面加工实验结果。在取值0.05mm步距是因为取点过密,加工的腕关节主身面不是由刀具连续切削面,切削时采用的碎直线段拟合逼近的方式,在步距比较小的情况下,因为重复切削,导致了表面质量的下降,当步距加大的情况下以为重复切削的减少,表面质量得到一定的提升,当行距大于刀尖圆弧半径一半的情况下,因为行距过大,表面质量会有所下降。加工中心的加工表面质量的Ra值一般在0.8—1.6之间,所以三种不同测量方式构建的模型在加工过程中对于φ8球头铣刀在步距0.15mm以下表面粗糙度都可以满足要求。#p#分页标题#e#
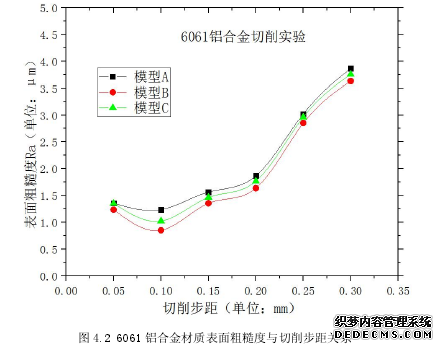
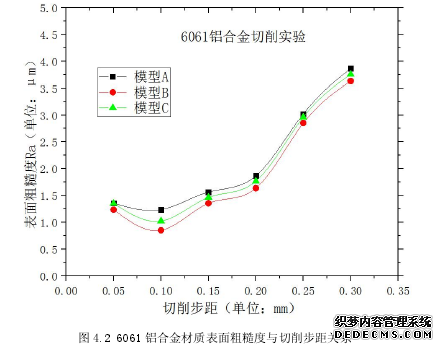
.........
结论
文章以工业机器人腕关节模型的逆向设计和数控编程加工为例,对腕关节样件模型进行了三维数据扫描、点云数据处理、用正向建模和快速拟合建模的方法进行逆向反求、分别对三组重构模型检测评价和数控加工工艺编排及自动编程研究。通过设定不同步距的四轴加工中心切削实验对三种不同方式构建的模型进行比对,评价出最优的曲面模型构建方法,切削步距主要影响的参数有加工精度、加工后零件部表面质量和加工时间,切削优化实验也主要根据这三个方面进行比对。最终得到以下结论:
(1)利用扫描仪对以工业机器人腕关节零部件为代表的复杂曲面类零部件进行扫描逆向,解决了自由曲面类零件建模难的问题,以处理过的腕关节点云数据为参照,运用正向建模方法即点—线—面的构建方式和快速拟合建模方法即面片拟合建模方式,使构建的腕关节零件模型整体符合要求。可根据实际需要选用不同的模型构建方法建立模型。
(2)通过腕关节模型的3D比较、2D比较和采样点的分析,可根据零部件自身的特征和客户的需求,选择恰当的曲面建模方法。当客户要求曲面无明显的交接痕迹,工期较短,零件表面整体较平滑光顺时,可选用快速拟合建模方式;当客户要求的产品几何特征明显,局部曲率变化范围大且要求偏差小或、精度高、表面质量好时,可选用常规正向建模方式。
(3)分析并制定出腕关节零部件的最优加工工艺并进行自动编程及后置处理,运用四轴加工中心按给定的切削步距做切削实验,对三组不同方式下构建的模型A、模型B、模型C进行多次切削,运用三坐标和粗糙度测量仪进行检测得出实验结果。
(4)四轴加工中心批量加工腕关节零件在不同切削步距对三种不同建模方式下的表面粗糙度检测结果,通过扫描逆向得到的两组腕关节零部件的表面粗糙度要优于借助普通量具测得数据构建的模型,三组模型切削步距设定在在0.1—0.2mm范围内整体的表面质量较好;分析K向和C向切削实验结果,得知模型A运用常规量具测得的尺寸构建的模型偏差较大,而扫描逆向得到的两组数据模型B和模型C偏差较小,通过扫描逆向正向思维构建模型C的制造偏差更小,此模型主身面构建的质量更优;分析切削步距对不同构建方式下得到的模型对总体加工时间的影响,三种模型加工时间接近,其步距在0.1—0.2mm选定效率会比较高。
..........
参考文献(略)