1 绪论
1.1 研究背景与意义
1.1.1 课题研究的背景
采煤机是现代化矿井最重要的采掘机械设备。由于煤炭产业的快速发展,采煤机具备的功能越来越丰富,相应的其自身构成模块愈加智能而复杂,因此对每个组件的加工生产要求标准也越来越高。2014 年 10 月,某煤机公司出口采煤机 MG650/1630-GWD 型采煤机截割部在完成装配后进行加载试验时,出现了严重的同轴度问题,具体表现为高速传动端异常噪音、震动及不合理的温度升高。一直以来,截割部壳体电机孔系的同轴度问题都严重制约着产品的可靠性。因此,迫切需要找出同轴度问题产生的原因,确定合理的解决方案,并彻底的予以杜绝。采煤机截割部示意图如图 1.1 所示,采煤机截割部的壳体是各种齿轮传动部件和组件的基础组成部分,它把数千个零件连接成一体,确保各个传动齿轮零件之间具有固定的相对位置和运动方式,组成一个输出低速、大扭矩的减速箱体部件[1]。减速箱体零件的结构形式和加工质量很大程度上决定了整个机械设备的使用性能,如使用寿命、传动效率及工作精度等[2]。采煤机截割部的主要作用是将电机的高速动力通过减速机构传递到低速截割滚筒上,以满足截割滚筒大扭矩负载的工作要求。截割部的传动形式为:电机—多级齿轮传动—行星减速机构传动—截割滚筒,其输入端电机额定转速一般为 1480r/min,而输出端滚筒转速一般为 30~50r/min,总传动比在 50~30 范围之间。由于截割煤层的耗损功率占用采煤机总功率的 80%~90%,因此要求截割部的传动结构具有较高的可靠性及传动效率[3]。电动机作为截割部的高速传动输入端,其工作情况的稳定性与可靠性将直接决定整个截割部的使用寿命,因此保证壳体安装电机部位的孔系加工精度尤其是孔系的同轴度误差就显得尤为重要。若孔系的同轴度偏差超过允许范围,则会在后期使用过程中会产生高温、噪音、振动、磨损等隐患,加速设备损坏[4]。在实际生产过程中,采煤机截割部壳体电机孔系长度一般大于 1m,孔径范围Φ260H7—Φ180H7—Φ665,为中间小,两头大的阶梯孔系,其特点是深、长、大,且孔系的形位公差同轴度精度要求较高。在具体生产过程中,影响电机孔系精度的因素较多,同轴度误差一般难以保证。本课题是对采煤机截割部壳体电机孔系的工艺加工方法及检测过程进行研究,找出同轴度误差产生的原因并加以优化和改进解决,进而保证孔系的同轴度误差要求。
...........
1.2 深长孔系加工方法研究现状
为了保证长距离且孔径较大的同轴孔系类零件的加工精度,需要同时对孔系的加工工艺和检测方法加以研究。当孔径大于 80mm 时,一般采用镗削加工[6]。针对基本尺寸和形位公差精度等级要求较高的大孔,镗削是最常见的加工方式[7]。但是,采用镗削方式加工孔时,若刀杆悬伸较长,会因重力而造成变形,刀杆悬伸端会产生严重的挠度变形。此外,刀杆伸出较大时,其尾部会产生颤动,这些因素均会严重影响孔的最终精度[8]。目前,国内外通用的孔加工方法主要有三种,分别是长刀杆镗孔法、镗模镗孔法(组合机床或专用镗床)和调头镗孔法[9]。长刀杆镗孔法该方法适应于单件、小批量的生产方式。将刀杆的刀柄端夹紧固定在主轴锥孔内,用支座或镗床设备的后立柱支撑刀杆的末端进行镗孔。镗孔时,主轴可同时作旋转和进给运动,也可采用镗轴做旋转运动而工件做进给运动的方法加工。但该加工方式的装夹方法较为繁琐,而且在装夹时容易使工件产生位移而影响孔的位置精度。此外,由于长刀杆因自重而造成中心轴线产生挠曲,导致工件上孔系的同轴度不易保证。
.......
2 采煤机截割部壳体深长孔系加工方法及误差分析
所谓深孔,就是指孔的长度与直径的比值大于 10 的孔,即 L/d≥10,常见的如转轴油孔、油缸内孔等。这类孔中,有的对加工精度和表面粗糙度要求较高,而且有的工件材料切削性能较差,这些因素常常成为生产中的一大难题[22]。本课题研究的深长孔系是指中间小、两头相对较大且总长度超过 1000mm 的孔系。相对于典型的深长孔,该孔的基本尺寸Φ665H7、深度 812mm 都超出常规孔的加工范围,既大又深,且配合精度为 IT7 级、同轴度误差精度为 6 级,在具体生产过程中,很难完全保证这些加工要求。随着机械制造技术与产品创新步伐的快速发展,新型产品结构的设计,对各类深孔加工的质量、效率以及刀具成本都提出了更为苛刻的要求[23]。结合我国目前机械加工的现状,在现有设备上不断提升加工技术,研究新型加工工艺已成为十分重要的课题。
2.1 截割部壳体零件图样分析
图 2.1 为西安煤机 C0N045301 截割部壳体电机孔系结构图,具体加工要求为:(1)材料 ZG25MnF8,调质处理,HB240~HB280,组织状态为回火索氏体。(2)轴承安装孔精度等级要求较高,加工时应严格予以保证。(3)Φ260H7 孔中心轴线对 Φ215H(7基准 C)孔中心轴线的同轴度误差为 Φ0.02mm,孔端面对基准 C 中心的垂直度误差为 0.05mm。(4)Φ663 孔中心轴线对 Φ665H7—Φ215H7(基准 C-C1)公共轴线的同轴度误差为Φ0.03mm,Φ665H7 孔轴线对 Φ665H7—Φ215H(7基准 C-C1)的同轴度误差为 Φ0.03mm。(5)工件毛坯不允许存在气孔、砂眼、包砂等铸造缺陷。
........
2.2 截割部壳体的技术要求
采煤机截割部壳体关键孔、平面的基本尺寸和形状位置公差将直接影响部件的整体性能,因此在壳体的结构设计中对此类重要部位的要求较为严格。截割部壳体示意图如图 2.2 所示。一方面截割部壳体具有高强度、高硬度的实际需求,另一方面壳体内腔结构复杂且尺寸要求高,毛坯生产选用易于成型的材料和制造方法,即采用铸造锰合金的方法。为了减少加工余量,当通孔直径大于 50mm 时,一般在毛坯上预先铸出小孔。此外,铸造生产毛坯时,应采取有效的措施避免产生气孔、砂眼、包砂等缺陷,并尽可能地减少铸造残余应力。截割部壳体壁厚不均、结构多变的特点,造成毛坯在铸造时不可避免地产生残存的内应力。为了去除残余的内应力,减小粗加工后的加工应力,确保后续加工精度的稳定性,一般在铸造毛坯及粗加工之后增加人工时效处理工序[24]。
.........
3 采煤机截割部壳体深长孔系加工方法优化...... 19
3.1 加工设备 ...... 19
3.1.1 原有加工设备参数及精度情况 .............. 19
3.1.2 现有加工设备参数及精度情况 .............. 20
3.2 同轴度精度等级优化 ........ 23
3.2.1 原同轴度精度要求 ............ 23
3.2.2 优化后同轴度精度要求 .... 24
3.4 本章小结 ...... 31
4 采煤机截割部壳体深长孔系同轴度测量方法改进..... 32
4.1 同轴度检测设备工作原理 ........... 32
4.2 三坐标测量仪的使用........ 34
4.2.1 测头校准 ..... 34
4.2.2 测量数据 ...... 36
4.3 截割部壳体深长孔系同轴度测量方法改进 ..... 37
4.3.1 增加同一基准孔的测量点及测量截面数量 ..... 37
4.3.2 增加测量孔截面的距离 .... 37
4.3.3 建立公共轴线 ......... 38
4.4 改进后同轴度误差测量结果验证 .......... 38
4.5 本章小结 ...... 40
5 结论与展望 .............. 41
5.1 结论 .............. 41
5.2 展望 .............. 41
4 采煤机截割部壳体深长孔系同轴度测量方法改进
同轴度误差的检测在机械制造过程中较为普遍,相应测量工具及测量方法的选择对测量误差大小的影响至关重要。
4.1 同轴度检测设备工作原理
三坐标测量仪是指 X、Y 和 Z 三个轴遵循右手笛卡尔坐标系,互相垂直布置,由 X、Y、Z 坐标值来确定工件上被测点空间位置的新型高效精密测量仪器。三坐标测量仪设备如图 4.1 所示。(1) 三坐标测量仪的机械结构① 结构形式三坐标测量仪是由三个正交的直线运动轴 X、Y、Z 构成的,它们的安装位置对设备的整体精度影响较大。② 导轨目前,大部分三坐标测量仪已采用空气静压导轨,它具有制造简单、精度高、摩擦力极小、工作平稳等许多优点。(2) 三坐标测量仪的测量系统标尺系统和测头系统两部分构成了三坐标测量仪的测量系统,它们决定着测量精度。测头用来采集信号,其性能直接影响三坐标测量仪的工作效率。(3) 测端对于接触式测头,测端是与被测工件表面直接接触的部分,一般称为探针;非接触式测头不需要接触零件表面,便可实现数据测量。针对各类结构不同的工件,需要选用不同的探针。一般情况下,探针应尽量短,减小变形。探针可以分为:直探针、星形探针、圆盘探针、圆柱探针、尖探针。现代三坐标测量仪都配备有计算机,由计算机来采集数据,通过运算输出所需要的测量结果。其软件系统功能的强弱直接影响到测量仪的功能和测量结果。#p#分页标题#e#
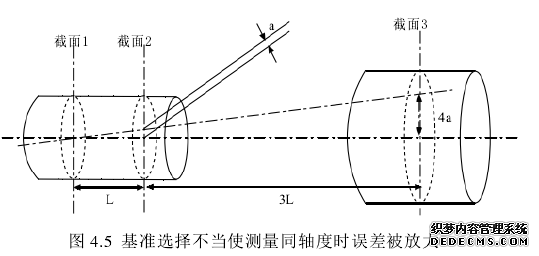
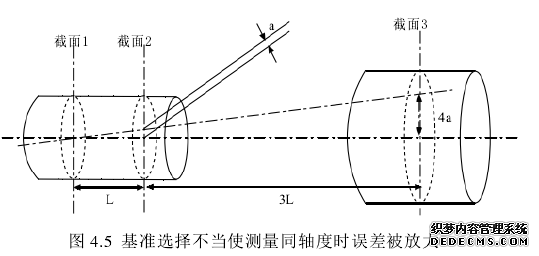
........
结论
本课题针对西安煤矿机械有限公司生产的采煤机截割部 N45301 壳体电机孔系在安装过程中出现的同轴度问题,对壳体的孔系加工方法及同轴度检测方法进行了研究。通过分析实际加工、测量过程中存在的不足,优化改进了截割部壳体深长孔系加工及测量方法,解决了同轴度误差超差的问题。通过研究得出了以下结论:
(1)针对采煤机截割部电机安装孔系存在的同轴度问题,通过分析孔系的技术要求及生产过程,确定孔系同轴度误差的主要影响因素为:工艺系统及工艺加工过程造成的累计误差和测量方式不合理造成的测量误差。
(2)通过对现有工艺加工方式的分析,提出了相应优化方法。针对加工余量过大造成后期应力变形的问题,提出了粗加工时,将原孔直径留余量 10mm 缩减为 8mm,平面留余量 6mm 缩减为 4mm,半精加工时孔直径留余量 4mm 缩减为 3mm,平面留余量 2mm缩减为 1mm;针对切削用量影响孔加工精度及粗糙度的问题,提出了“快速轻切削”的加工理念,并且通过大量现场试验总结,规范了不同孔径加工时的切削参数(吃刀量、主轴转速、进给量)标准;针对工件装夹时存在的夹紧变形问题,设计专用工艺基准垫块,减少了工件压紧力变形;针对调头镗孔时的基准孔找正存在的误差问题,明确了找正基准部位,规范了找正基准孔的先后顺序及找正允许误差。
(3)通过对现有测量方法的过程研究,提出了相应改进方案。针对测量基准孔上截面及测量点的位置选取不当造成测量误差偏大的问题,提出了增加同一基准孔的测量截面数量、增加测量孔截面的距离和建立公共轴线的方法,确保了测量结果准确反映孔系同轴度误差的真实情况。
(4)通过采用优化改进后的工艺加工方法和测量方法,经过现场大量验证,实际测量所得的孔系同轴度误差明显优于前值,且小于技术标准值。
..........
参考文献(略)