本文是一篇工程论文,工程论文论文是学术作品,因此其表述要严谨简明,重点突出,专业常识应简写或不写,做到层次分明、数据可靠、文字凝练、说明透彻、推理严谨、立论正确,避免使用文学性质的或带感情色彩的非学术性语言。论文中如出现一个非通用性的新名词、新术语或新概念,需随即解释清楚。(以上内容来自百度百科)今天上海论文网为大家推荐一篇工程论文,供大家参考。
第 1 章 绪论
1.1 引言
汽车自进入工业领域已百余年,生产能力逐步提升、性能不断优化,在经济领域中占有重要地位。其产品的更新换代,新技术的不断加入,已使之成为衡量一个国家工业及技术发展水平的重要指标。随着大批量流水线式生产,现阶段汽车保有量已趋于饱和,加之传统汽车动力一直采用非再生能源,促进汽车工业向环保化、节能化、美观化、轻量化方向发展。汽车正常是由发动机、汽车底盘、车身和电气系统等部分组成[1]。车身作为汽车的重要组成部分,彰显了汽车优质设计和制造的完美性,在功能一致情况下,视觉体验已成为最大需求,也是提升各大汽车制造商市场竞争力的重要手段。如图 1.1所示,车身覆盖件一般指车外表面和驾驶室内表面零件,如前围、后围、侧围、顶盖、车门、发动机罩、后备箱盖等[2]。在整车产品零部件中汽车覆盖件约占至 60%以上,其具有难于成形、尺寸高精度、材料薄等特点[3],基于以上特点,冲压成形因工艺操作简单,生产效率高,易于实现机械化和自动化生产,必然是成形工艺的首选,汽车覆盖件复杂的形状和精度要求也能通过优质的模具设计得以实现。模具作为汽车覆盖件的冲压成形工具,其生产周期占到整车开发时间的 70%以上,它的合理设计和制造品质直接影响零件的质量和汽车外观整体品质。众所周知,产品的推陈出新是提高市场竞争力的有效方法,基于模具在整车开发的重要性和所占的时间比例,缩短模具的制造周期是各大汽车制造商急需解决的问题。传统模具设计制造由于技术发展水平等因素限制,其开发过程的制约因素很多。在结构设计方面:我国此方面起步较晚,设计水平相对较低,结构不合理现象时有发生,并且设计经验不足,设计修改效率低;在冲压工艺方面:由于设计和制造水平的限制,模具成型精度低,并且采用试错法,反复试模调整才能达到需求标准;在制造调试方面:制造设备落后,难以保证加工精度并且过度依赖工程师的经验。以上致使模具开发周期时间长、原材料耗损严重、增加开发成本。在日趋激烈的市场竞争中,继续采用传统的开发方式已然不能满足各大汽车企业制造商的需要,基于此寻求新的解决方案已迫在眉睫。
.........
1.2 冲压成形工艺介绍
冲压是指借助冲压设备提供动力,使模具里的金属板材受变形力作用制成各种片状零件、壳体等拥有一定尺寸、形状及性能的产品生产技术。根据加工所使用温度的不同,可将冲压成形加工分为冷冲压和热冲压两种[11]。1)冷冲压:在室温条件下,使用模具在压力机作用下将金属板料产生塑性变形或分离,从而获得所需零部件的加工方法,简称为冲压。冷冲压适用于表面状态要求高、薄板材加工。2)热冲压:是将板料加热至奥氏体化状态,快速转移至模具中高速冲压,在保证一定压力的情况下,以 20~300℃/s的冷却速度进行淬火处理,保压淬火一段时间以获得具有均匀马氏体组织构件的成形方式。热冲压适用于变形抗力大、塑性变形较差的板材加工。
.........
第 2 章 板料成形过程数值模拟基本理论
2.1 引言
所谓板料冲压成形过程就是在外力的作用下,依靠模具对材料挤压而成形的一种大变形、大位移、大转动塑性加工法。其过程理论上涉及多重非线性耦合问题,同时也包含很多复杂的物理现象,如涉及接触碰撞现象、塑性变形现象、摩擦磨损现象等,先期板料成形都是模具加工后试制才将问题暴露出来,经过大量的实验和多年的研究以及有限元技术的不断应用,总结出来有限元的相关理论知识。
........
2.2 单元理论
在板料成形数值模拟过程中,所选用的模拟单元类型将对模拟的精度与模拟计算过程都有很大影响,而在单元分类方面可分为薄膜单元、实体单元和壳单元[43]。薄膜单元该基于二维薄膜理论的单元类型是最早使用于成形模拟中的单元,单元构造简单、计算模拟所需要的内存小,且未对弯曲效应和横向剪切等进行考虑,该模型认为应力均匀分布于厚度方向并平行于中性面[43]。因此,该种模型单元仅适用于分析对弯曲变形不明显且精度要求不高的板料成形过程.基于薄膜单元的不足,提出基于连续介质理论的三维实体单元,不仅结构简单还可以分析弯曲变形和横向剪切变形、模拟精度高。但在板料冲压分析时,若采用实体造型,根据实体单元自身的特点,会将板料的网格划分的很细避免的产生刚度奇异矩阵,致使计算时间长计算效率低。正常情况下,若无利用实体单元的特殊要求,板料成形过程中并不采用实体单元进行模拟分析。现今,壳单元是板料冲压成形数值模拟过程中使用最为普遍的模型。壳单元是基于板壳理论,可以分析弯曲变形和横向剪切变形,模拟精度高,计算效率也远远高于实体单元。
........
第 3 章 助力器复杂前壳体成形性分析....21
3.1 零件成形性分析...........21
3.2 冲压成形工艺.......22
3.3 助力器复杂前壳体冲压成形工艺参数计算......... 26
3.4 有限元模型的建立 ...... 29
3.5 模拟成形问题的研究........... 31
3.6 本章小结 ..... 35
第 4 章 助力器复杂前壳体数值仿真模拟及优化..... 37
4.1 引言..... 37
4.2 成形极限图.......... 37
4.3 零件模型的建立.......... 39
4.4 板料模型的设置.......... 41
4.5 模拟参数的设置...........43
4.6 模拟参数的优化...........45
04.7 本章小结.......50
第 5 章 助力器复杂前壳体翻孔模拟及优化.....51
5.1 预冲孔模拟模型建立 ...........51
5.2 预冲孔模拟优化...........51
5.3 实际应用.......54
5.4 压力机吨位的选择........55
5.5 本章小结 ......56
第 5 章 助力器复杂前壳体翻孔模拟及优化
5.1 预冲孔模拟模型建立
由 3.3.3 冲孔翻边高度的计算可知,对助力器复杂前壳体拉延过程结束后需对其进行冲孔然后再完成翻边工艺。而预冲孔直径大小直接影响翻边高度能否满足需求,因此,本章着重讨论预冲孔大小和翻边过程的模拟优化。由图 5.2 可知,当预冲孔直径取 3 1.43mm 时,翻边后边缘位置部分出现处于破裂临界区的黄色,但未出现产生破裂的红色区域,说明材料在翻边工序结束后未发生破裂。当预冲孔直径取 28.5mm时,翻孔高度增加,满足助力器复杂前壳体翻边高 h 8.4mm的要求。与理论计算保持一致,并且在计算过程中考虑了安全系数,在计算预冲孔 29.185mm 为极限破裂临界值,当预冲孔直径为 28.5mm 在理论计算中将产生破裂现象,但在数值模拟过程中,破裂区域发生在边缘而且范围很小,几乎不影响质量要求,并且破裂区域在满足翻边高度的前提下可以通过修边方式进行处理,由此助力器复杂前壳体可通过预冲孔 28.5mm 翻边一次成形。
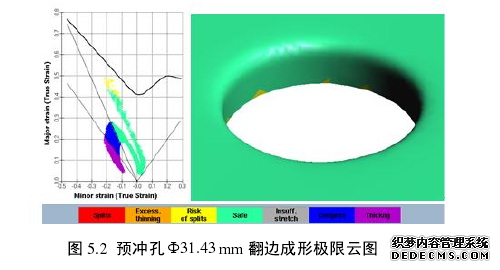
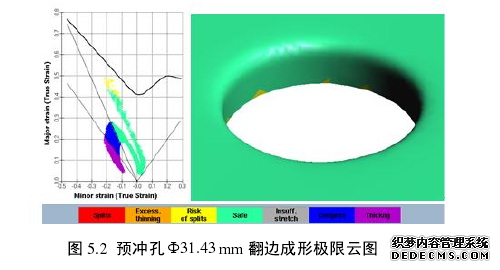
.........
结论
本文是利用 AutoForm 软件对助力器复杂前壳体的冲压成形过程进行数值模拟,需要根据实际生产情况研究其拉延成形性和翻边过程。对其可能在成形过程中出现的成形缺陷进行预测,通过有效的办法对设计进行优化,进一步对其进行控制,得到高质量的冲压产品,降低开发周期和生产成本。本文对以下工作着重研究:(1)冲压成形过程中坯料与凸凹模接触,在凸凹模型腔中受成形力的作用下完成成形过程,在受力不均或其他状况下造成成形缺陷,对成形缺陷的形成机理及控制方法进行研究;(2)冲压成形的研究方法,从最初的解析法和实验法,到现如今使用的有限元分析法,其各自的优势和缺点进行研究;(3)关于有限元数值模拟单元,由过去精度较低的薄膜单元与实体单元逐步发展而来的壳单元是当前最为广泛使用的有限元数值分析单元,模拟过程中分析计算效率得到大幅度提高;(4)关于有限元模拟求解算法方面的研究,静力隐式算法具有高计算精度但计算量、时间消耗大的特点,动力显式算法耗时短但无法保证计算精度,而静力显式算法的计算效率和计算精度都不是很高,所使用的一步成形法目前只适用于对零件成形进行初步的分析,本文使用的 AutoForm 软件是通过静力隐式算法多冲压过程进行模拟计算;(5)接触算法的研究使有限元理论计算结果更加接近实际生产,罚函数接触算法精度低不适合有限元模拟分析回弹使用,拉格朗日接触算法计算精度高但对网格形状质量要求也高,非线性罚函数接触算法计算精度高并且定网格要求低,目前在有限元数值模拟理论计算此方法可大大提高计算精度。#p#分页标题#e#
..........
参考文献(略)