本文是一篇电力论文,电力系统各种电压等级均通过电力变压器来转换,电压升高为升压变压器(变电站为升压站),电压降低为降压变压器(变电站为降压站)。一种电压变为另一种电压的选用两个线圈(绕组)的双圈变压器,一种电压变为两种电压的选用三个线圈(绕组)的三圈变压器。(以上内容来自百度百科)今天为大家推荐一篇电力论文,供大家参考。
1 绪论
近年来,随着自然环境的日渐恶化,电力电子装置高效、节能化的趋势已不可阻挡,其中感应加热电源以非直接接触、加热效率高、加热速度快、控制自动化、环保节能等特点被广泛的应用在金属表面热处理、淬火、熔炼、热套、冶金、管材焊接和废气处理等场合【2】。感应加热技术从上世纪初就被应用在工业上,为了降低电源成本、提高效率,感应加热技术朝着高频化、智能化和复合化的方向发展,随着技术的日渐成熟,将会和各行各业建立密切关系,应用更加广泛。
1.1 感应加热的原理与三大效应
现代感应加热的基本理论来源于 Michael Farady 提出的电磁感应定律,即在闭合的初级线圈中通以交变电流,会在工件内部产生感应电流(相当于闭合的次级线圈),感应加热是将电能通过电磁感应的方式转化为热能作用在工件上,从而达到加热的目的。在图1-1 中,一定频率的交变电流 iH流入感应线圈中,将会产生与 iH同频率的交变磁通 ,生成的感应电动势 e 作用在工件上,进而形成感应电流 ie,但金属工件内部有电阻 R 存在,会引起金属体发热【3】【4】。从以上各式可以看出:当负载电感和电阻一定时,感应加热装置的热功率与被加热线圈的频率 f 和磁通密度 m有关。而磁通密度是由流过感应加热线圈上的电流大小所决定,因此可通过控制流过感应加热线圈上的电流大小,改变金属工件的加热温度;同样,改变被加热线圈的频率也能改变流过感应加热线圈上的电流大小,从而改变感应加热装置的热功率。此外,金属工件的截面大小、截面形状以及磁导率等,都对会影响感应加热线圈上的电流,进而影响工件的加热效果【3】。
........
1.2 课题的研究背景
1.2.1 负载特性
感应加热中,加热线圈和加热工件常被等效为电感和电阻串联的形式,如图 1-2 所示,感应线圈当做一次绕组,工件为二次绕组,将其等效为变压器,其中 R1、L1为加热线圈的电阻与电感,R2、L2为工件的电阻与电感,Req和 Leq为折算后的等效电阻和等效电感【5】。为了提高电源的工作效率,加入谐振电容,与等效电感和电阻串联构成负载槽路。不同的工件所等效的负载参数各不相同,在感应加热电源的工业现场,工作状况比较复杂,加热对象各式各样,例如在管材焊接场合,管材的直径大小和长度均会影响等效负载电感和电阻,因此负载参数大小难以确定,对负载匹配带来很大难度。由于相对磁导率和电阻率会随温度发生变化,尤其是在熔炼、废气处理等一些需要加热到居里点温度(700℃)以上的场合,磁导率会发生突变,变化趋势如图 1-3 所示【5-7】,所以感应加热的负载参数电感和电阻在加热过程中会随温度的升高而变化。由公式(1.7)和(1.8)可知负载电感与磁导率成正比,负载电阻与电阻率成正比,但在实际加热过程中负载等效电感和电阻还受到电磁感应、集肤效应及介质特性等因素的影响,电感和电阻均在居里温度点之前缓慢上升,到达居里点之后,电感和电阻突变减小。因为相对导磁率突变减小时,会减弱集肤效应程度,使得涡流分布在加热工件的各个层面,导致阻抗面增加,所以电阻也会突变减少【5】。
........
2 负载参数辨识方法的分析
2.1 感应加热主电路分析
本研究主要针对熔炼和废气处理等一些负载参数变化较大的中频感应加热电源,主电路拓扑一般为全桥逆变电路如图 2-1 所示。目前在很多研究领域中都追求智能化,电力电子的应用也不例外,在许多控制中均采用优化算法,如在感应加热电源的调功控制中用到模糊控制算法,遗传算法等等,而在关于控制方法进一步量化的研究中,有一些寻优算法被广泛使用,如最小二乘法、粒子群算法、蚁群算法和退火算法等等。在电力电子中,这些算法主要是用来解决系统参数辨识问题,而本文主要是将最小二乘法进行优化,应用在感应加热中解决负载参数变化的问题。
......
2.2 算法分析
在实际应用中受到噪声的影响,当遗忘因子μ取的越大,可以降低干扰信号的影响,减小数据变化过程中的误差,提高辨识系统稳定性,但收敛速度会降低;当遗忘因子μ取的越小,可以减小历史数据的影响,凸显当前数据的作用,提高系统的辨识能力,但是计算结果对干扰信号敏感,带来较大误差。根据感应加热负载的实际变化情况,使遗忘因子可变,当感应加热负载参数变化不明显时,增大遗忘因子μ,提高抗扰能力;当负载参数变化剧烈时,减小遗忘因子μ,加快收敛速度【12】【31】【33】。
............
3 负载参数在线辨识的仿真验证与分析............15
3.1 仿真结果分析............15
3.2 频率跟踪与功率控制仿真............17
3.3 本章小结..........19
4 基于 FPGA 和 STM32 的控制系统设计.........20
4.1 软件设计..........20
4.1.1 软件简介...........20
4.1.2 程序设计...........21
4.2 检测和保护电路设计..........27
4.2.1 采样电路设计.............27
4.2.2 逆变器驱动电路及保护电路.........28
4.3 本章小结..........29
5 实验结果与分析........30
5.1 实验平台..........30
5.2 实验结果分析......31
5.3 本章小结.............35
5 实验结果与分析
5.1 实验平台
为了验证上述方案的可行性,搭建了基于FPGA和ARM的感应加热电源的实验平台,其中主电路拓扑如图 5-1 所示,负载参数如表 5-1 所示。主电路由整流电路、滤波电路和逆变电路三部分构成。电源的工作过程为将输入的工频电通过整流变成直流电,再经过滤波器滤波送到逆变电路转化成所需要频率的交流电供给负载。由于该电源为中频感应加热电源,工作频率为 10kHz 左右,所以开关器件选用IGBT,整流部分为不控整流电路,因此直接采用整流模块。负载参数的辨识误差会对电路的工作状态和功率产生影响,其中电阻的变化会导致功率变化,而电感的变化会影响谐振频率,最终影响加热效率和加热效果。在感应加热的实际加热过程中,最终的加热效果是由温度直接决定的,受外界客观因素影响较大,因此其容错率较高,误差在±5%以内即可满足大多场合的要求。在加热时间方面,由于加热对象的不同,加热周期也各不相同,例如对小工件进行焊接时只需几秒即可完成,而在一些工业应用的场合如熔炼场合等需要 1 个小时以上的时间。在负载参数会发生突变的场合,加热工件以 45#钢为例,其磁导率随温度变化如表 5-2 所示,温度在 700 度到 760 度之间变化率剧增,负载参数发生突变,在大功率加热时,从 700 度到 760 度需要几秒钟时间,所以计算速度越快对电路的影响越小。
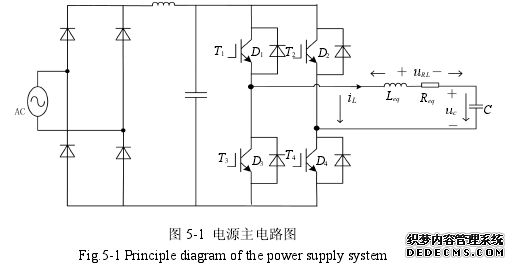
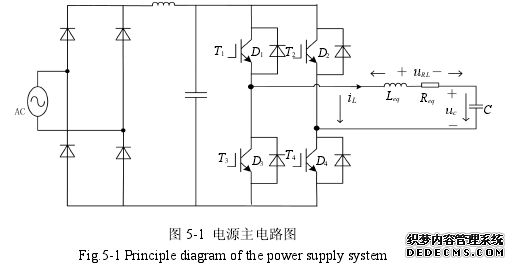
........
总结
本文针对感应加热负载参数难以确定以及居里点处突变的特性,分析了串联负载谐振电路负载参数辨识的方法,对递推最小二乘法进行优化,将其应用在感应加热场合中,解决感应加热负载特性带来的问题,最终通过理论分析,仿真验证以及实验结果得出该方法可以被用来解决感应加热负载参数变化所带来的问题。在本文中,所做的主要工作如下:
(1)分析了感应加热负载特性,以及加热过程中负载变化可能带来的问题,尤其是在居里点处负载突变的原因和造成的后果。
(2)建立感应加热电源负载槽路的方程模型,列出负载参数与负载槽路中各电压和电流的关系式,介绍负载参数的辨识方法。
(3)介绍了最小二乘法的基本原理和优缺点,并对其根据感应加热负载的特性进行优化,着重解决负载参数突变时的辨识工作。
(4)根据理论分析的方案,在 MATLAB 中搭建了仿真模型,验证了理论分析的结果,并针对实际存在的问题进行了各种工况的仿真,通过对算法的优化,实现了各种工况下负载参数的准确辨识。(5)设计了感应加热电源的控制电路。按照设计要求,设计了控制电路、采样电路以及相应的过流保护电路。同时,依据感应加热负载辨识的要求,使用 ARM 完成采样、PWM 脉冲、数据传输等功能。在 FPGA 中完成了核心算法的计算。#p#分页标题#e#
(6)依据设计要求,搭建了感应加热实验平台的主电路和控制电路,编写相应的控制和算法程序,从实验上验证了本文所述辨识方案的可行性。
(7)最后完成了频率跟踪与直流侧调功的闭环实验,进一步验证了该方案可以通过对负载参数的辨识去控制频率和功率,能达到调高加热效率和改善加热效果的目的。
..........
参考文献(略)